Structural Elements
An important aspect of geomechanical analysis and design is the use of structural support to stabilize a rock or soil mass. Structures of arbitrary geometry and properties, and their interaction with a rock or soil mass, can be modeled with FLAC3D. This section describes the types of structural-support members (beams, cables, piles, shells, geogrids and liners), or structural elements, available in FLAC3D, as well as the numerical formulation that supports the structural-element logic.
The structural elements can either be independent of, or coupled to, the grid representing the solid continuum. The structural-element logic is implemented with the same explicit, Lagrangian solution procedure as the rest of the code (as opposed to an implicit, matrix-inversion procedure): the full dynamic equations of motion are solved, even for modeling processes that are essentially static. Large displacements, including geometric nonlinearity, can be accommodated by specifying a large-strain solution mode; and the full dynamic response of the system in the time domain can also be obtained with the dynamic-analysis option.
This overview section is organized as follows. We begin with a brief description of the six types of structural-support members provided by FLAC3D. This is followed, in Terminology, by a high-level introduction describing the relevant terminology. The means by which structural elements are created and joined to one another is discussed next (in Geometry Creation} and Joining Structural Elements). The discussion includes a description of how particular physical entities (e.g., physical beams) that are composed of a collection of beam structural elements and nodes can be referred to — for purposes of plotting and specification of property and boundary conditions — as a single unit. The general procedures are also described for specification of boundary and initial conditions (in Specifying Boundary and Initial Conditions), stresses in shells (in Stresses in Shells), coordinate systems and sign conventions (in Local Systems and Sign Conventions), damping conditions (in Specifying Damping and Timestep Conditions), thermal expansion (in Thermal Expansion in Structural Elements) and material properties (in Material Properties).
It is helpful to discuss the various conditions that can be prescribed at structural nodes before describing each of the types of structural elements in FLAC3D. This is done in Structural Element Nodes. This section also includes a summary of the commands associated with nodes.
Each type of structural element is then described in detail in Beam, Cable, Pile, Shell, Geogrid, and Liner Structural Elements. This includes a description of the mechanical behavior, the required properties and associated commands. Finally, simple examples are included at the end of each section, illustrating the application of each structural-element type.
A detailed discussion of the general formulation of the structural-element logic in FLAC3D is provided in General Formulation of Structural-Element Logic. Users wishing to implement more complex interaction between structural elements and the grid should consult this section to gain an understanding of the implementation procedure.
Throughout this section, matrices and vectors will be denoted by boldface type. The mathematical symbols \([\quad ]\), \(\lceil\quad\rfloor\), \(\{\quad\}\) and \(\lfloor\quad\rfloor\) will designate a rectangular matrix, diagonal matrix, column vector and row vector, respectively. Also, structure and element matrices will be described by uppercase and lowercase English alphabet characters. For example, \([\bf K]\) and \([\bf k]\) designate structure and element stiffness matrices, respectively.
Types of Structural Elements
Six forms of structural-support members can be specified. Each of these members can be joined to one another and/or the grid.
- Beam Structural Elements — Beam structural elements are two-noded, straight, finite elements with six degrees of freedom per node: three translational components, and three rotational components. A physical beam (i.e., an arbitrarily curved, beam structure of isotropic material and bisymmetrical cross-section) can be modeled as a collection of beam elements. Each element behaves as a linearly elastic material with no failure limit; however, it is possible to introduce a limiting plastic moment, or even a plastic hinge (across which discontinuity in rotation may develop), between elements. Beam elements may be rigidly connected to the grid such that forces and bending moments develop within the beam as the grid deforms, and they may be loaded by point or distributed loads. Beam elements are used to model structural-support members in which bending resistance and limited bending moments occur, including support struts in an open-cut excavation and general framed structures loaded by point or distributed loads.
- Cable Structural Elements — Cable structural elements are two-noded, straight, finite elements with one axially oriented translational degree-of-freedom per node. A physical cable (i.e., an arbitrarily curved, cable structure of isotropic material) can be modeled as a collection of cable elements. Each element can yield in tension or compression, but cannot resist a bending moment. A shear-directed (parallel with the cable axis) frictional interaction occurs between the cable and the grid. A cable may be anchored at a specific point in the grid, or grouted so that force develops along its length in response to relative motion between the cable and the grid. Cables may also be point-loaded or pretensioned. Cable elements are used to model a wide variety of structural-support members for which tensile capacity is important, including cable bolts and tiebacks.
- Pile Structural Elements — Pile structural elements are two-noded, straight, finite elements with six degrees of freedom per node. A physical pile can be modeled as a collection of pile elements. The stiffness matrix of a pile element is identical to that of a beam element; however, in addition to providing the structural behavior of a beam, both a normal-directed (perpendicular to the pile axis) and a shear-directed (parallel with the pile axis) frictional interaction occurs between the pile and the grid. In this sense, piles offer the combined features of beams and cables. In addition to skin-friction effects, end-bearing effects can also be modeled (see Axially Loaded Pile). Piles may be loaded by point or distributed loads. Pile elements are used to model structural-support members, such as foundation piles, for which both normal- and shear-directed frictional interaction with the rock or soil mass occurs.
A special material model is also available as an extension to the pile element to simulate the behavior of rockbolt reinforcement. This model includes the ability to account for changes in confining stress around the reinforcement, strain-softening behavior of the material between the structural element and the grid, and tensile rupture of the element.
- Shell Structural Elements — Shell structural elements are three-noded, flat finite elements. Five finite-element types (2 membrane elements, 1 plate-bending element and 2 shell elements) are available. A physical shell (i.e., an arbitrarily curved, shell structure of either isotropic or orthotropic material) can be modeled as a faceted surface composed of a collection of shell elements. The structural response of the shell is controlled by the finite-element type (to resist membrane loading only, bending loading only, or both membrane and bending loading). Each shell element behaves as an isotropic or orthotropic, linearly elastic material with no failure limit; however, one can introduce a plastic-hinge line (across which a discontinuity in rotation may develop) along the edges between elements, using the same double-node procedure as is applied to beams. Shell elements may be rigidly connected to the grid such that stresses develop within the shell as the grid deforms, and they may be loaded by point loads or surface pressures. Shell elements are used to model the structural support provided by any thin-shell structure in which the displacements caused by transverse-shearing deformations can be neglected.
- Geogrid Structural Elements — Geogrid structural elements are three-noded, flat, finite elements that are assigned a finite-element type that resists membrane but does not resist bending loading. A physical membrane can be modeled as a collection of geogrid elements. The geogrid elements behaves as an isotropic or orthotropic, linearly elastic material with no failure limit. A shear-directed (in the tangent plane to the geogrid surface) frictional interaction occurs between the geogrid and the FLAC3D grid, and the geogrid is slaved to the grid motion in the normal direction. A geogrid can be anchored at a specific point in the FLAC3D grid, or attached so that stress develops along its surface in response to relative motion between the geogrid and the FLAC3D grid. The geogrid can be thought of as the two-dimensional analog of a one-dimensional cable. Geogrid elements are used to model flexible membranes whose shear interaction with the soil are important, such as geotextiles and geogrids.
- Liner Structural Elements — Liner structural elements are three-noded, flat finite elements that can be assigned any of the five finite-element types available for shell elements. A physical liner can be modeled as a collection of liner elements that are attached to the surface of the FLAC3D grid. In addition to providing the structural behavior of a shell, a shear-directed (in the tangent plane to the liner surface) frictional interaction occurs between the liner and the FLAC3D grid. Also, in the normal direction, both compressive and tensile forces can be carried, and the liner may break free from (and subsequently come back into contact with) the grid. Liner elements are used to model thin liners for which both normal-directed compressive/tensile interaction and shear-directed frictional interaction with the host medium occurs, such as shotcrete-lined tunnels or retaining walls.
An option that allows interaction with the FLAC3D grid on both sides of the liner is available with the liner element.
Terminology
With the addition of structural-element logic, FLAC3D can model the structural response of a mechanical system that is composed of a solid continuum and a framework of load-carrying members. The solid continuum is represented by a collection of polyhedral-shaped zones, each of which is associated with a set of gridpoints. The framework is represented by a collection of structural elements, each of which is associated with a set of nodes. The framework interacts with the solid continuum by means of links which connect nodes to zones (not simply to gridpoints) or to other nodes.
Six degrees of freedom, composed of three translational components and three rotational components, are associated with each node. Each node also has its own local orthogonal coordinate system. The node-local system provides the directions in which the equations of motion for the node are solved, and also defines the directions in which the node can be attached to a target entity via a link. A link supports the following three attachment conditions, which are specified independently for each local direction of its source node: free, rigid and deformable. See Structural-Element Links for a detailed description of structural-element links.
For most modeling situations, it is not necessary to specify link properties; instead, it is sufficient to create, position and assign properties to the desired structural elements. Nodes (and links, if necessary) will be created automatically, and will inherit necessary information from the structural elements that use them.
Geometry Creation
The six types of structural elements provide the building blocks, or components, needed to model six types of physical items: beams, cables, piles, shells, geogrids and liners. Each physical item is associated directly with a collection of component objects of the same type. For example, a cable is associated with a collection of cable elements, whereas a liner is associated with a collection of liner elements. The association between physical items and their corresponding component objects is implemented by storing two distinct identification numbers for each structural element:
- id — The ID number refers to the physical item.
- component-id — The component-ID number refers to the component object itself.
Properties may be specified for each type of physical item, and will be inherited automatically by the associated component objects. For example, the command
struct cable property grout-friction=30.0 range id=3
will assign a grout friction angle of 30 degrees to all cable elements thar are part of the cable with an ID number of 3, whereas the command
struct cable property grout-friction=30.0 range component-id=3
will assign a grout friction angle of 30 degrees to the single cable element with a component-ID number of 3.
The Beam, Cable, Pile, Shell, Geogrid, and Liner plot items allows one to view the six different element types, as well as the nodes and the links.
Beam, Cable and Pile Structural Elements
The geometry of beams, cables and piles is defined by their corresponding collection of component objects. The creation commands for all three of these types are identical, and for simplicity the following examples will be for cable elements, but they will work just as well for pile or beam elements.
A single cable forming a straight line (made up of a number of individual elements) can be created using the structure cable create
command, in one of three ways:
- By specifying the two end locations (
structure cable create by-line
),- By specifying the ID numbers of two nodes at each end (
structure cable create by-nodeids
), or- By specifying a starting point, a direction, and a length (
structure cable create by-ray
).
Each create command takes an optional ID argument to denote the ID of the item to be created. If no ID is provided, the next available ID will be used. New nodes are created automatically at uniformly spaced internal points along the line. If a node already exists at one of the end locations and is used by a element with the same ID as that given in the command, a new node is not created at this location; otherwise, a new node is created.
A group of cables may be created from external geometric information, using the structure cable import
command. For each line segment in the imported data, one or more cable elements will be created. Current, data can be imported in one of three ways:
- From an existing geometry set (
structure cable import from-geometry
). See the Geometry for details of creating a geometric set.- From a compatible CAD file (
structure cable import from-file
). The currently compatible file types are DXF, STL, and the Itasca Geometry format.- From an extruder set (
structure cable import from-extruder
). See the Extrude for how to use the 2D Extruder.
The following example, depicted in Figure 1, illustrates the association mechanism between nodes and structural elements. The nodes are not drawn in these plots. Instead, the cable elements are drawn at 90% of their true length. Consider a curved cable, identified by an id of 5, that is composed of a collection of 7 elements and 8 nodes. Each element stores the cable id of 5, as well as its own unique component-id. This can be seen by moving the mouse over an element and examining the information window. In this way, the 7 elements are combined to form a complex, arbitrarily curved cable that can be referred to by the single id of 5.
The commands necessary to produce the model are shown in Figure 1 are given in selexample1-1.f3dat.
selexample1-1.f3dat: Creating a single curved cable identified by an ID of 5
model new
model largestrain off
struct cable create by-line (0.0,4.0,0.0) (3.0,4.0,0.0) segments=2 id=5
struct cable create by-line (3.0,4.0,0.0) (6.0,3.0,0.0) segments=3 id=5
struct cable create by-line (6.0,3.0,0.0) (9.0,1.0,0.0) segments=2 id=5
;plot create 'SELId'
;plot item create struct cable label id width 4 shrink 0.9 addlabel '5' black
;plot item create axes scale 15
;plot view center (4.5,2.525,0) eye (4.5,2.525,12.798) roll 90
;plot 'SELId' export bitmap filename "114F0005.png"
There is no restriction that requires the end locations to lie within the FLAC3D grid; in fact, it is not necessary to have a grid at all. (Recall that the structural elements can either be independent of, or coupled to, the grid representing the solid continuum.) When using the structure cable create
command, if any of the nodes used by the newly created elements lie within zones, these nodes will be linked to these zones, and the link properties will be set consistent with the corresponding element behavior described in Beam, Cable, and Pile Structural Elements.
The most common reason to specify more than one segment between end locations is to improve accuracy, especially with piles and cables that are interacting with the host medium. In this case, the distribution of shear forces along each pile or cable is a function, to some extent, of the number of nodes. The following rules-of-thumb have been used to determine the number of nodes to use when modeling cables:
- Try to provide approximately one node in each FLAC3D zone. The reasoning here is that since the zones are constant-stress regions, it is not necessary to have more than one interaction point within a zone.
- Try to provide two to three cable element within the development length of the cable. The development length of the cable is determined by dividing the specified yield strength, \(F_t\), by the grout cohesive strength, \(c_g\). By following this procedure, failure by “pull-out” can occur if such conditions arise. If the cable elements are too long, then only the yield failure mode of each element is possible. (This reasoning also applies to pile elements if used to simulate the behavior of rockbolts.)
Shell, Geogrid and Liner Structural Elements
The geometry of shells, geogrids and liners is defined by their corresponding collection of component objects. The creation commands for all three of these types are identical, and for simplicity the following examples will be for shell elements, but they will work just as well for geogrid or liner elements.
A single shell surface (made up of a number of individual elements) can be created using the structure shell create
command, in one of four ways:
- By specifying a set of surface zone faces, on which elements will be created (
structure shell create by-face
).- By specifying four existing structural nodes, forming a quadrilateral (
structure shell create by-nodeids
).- By specifying four points in space, forming a quadrilateral (
structure shell create by-quadrilateral
).- By specifying three points in space, forming a triangle (
structure shell create by-triangle
).
A shell surface may also be created from external geometric information, using the structure shell import
command. For each line segment in the imported data, one or more shell elements will be created. Current, data can be imported in one of two ways:
- From an existing geometry set (
structure shell import from-geometry
). See the Geometry for details of creating a geometric set.- From a compatible CAD file (
structure shell import from-file
). The currently compatible file types are DXF, STL, and the Itasca Geometry format.
The most common way that shell-type elements are created in FLAC3D is with the structure shell create by-face
command, which places them on zone faces. As an example below, the geometry logic is used to create a 45 degree arc surface of shell elements. The command used as listed in selexample1-2.f3dat.
The geometry edge create by-arc
command is used to create a 45 arc section in 8 segments. Then the geometry generate from-edges
command is used to extrude those edges in the y-direction into 8 segments. This description is then used by the structure shell import from-geometry
command to create two triangular shell elements per quadrilateral in the geometric description. Figure 2 shows the resulting shell elements.

Figure 2: Representation of a curved shell created by generating shell elements using a geometry description
Joining Structural Elements to One Another and to the Grid
Structural elements can be joined to one another either by sharing a node or by having one of their nodes linked to either another node or to a zone (see Terminology). If two or more structural elements share a node, all forces and moments are transferred between the elements at the node. If it is necessary to limit or eliminate specific forces and/or moments that are transferred between elements, then two separate nodes may be created and connected by a node-to-node link, and the appropriate attachment conditions set. For example, if it is necessary to join two beams with a ball-joint, a node-to-node link can be added between the two beam end nodes, and the attachment conditions set in all translational and rotational directions to be rigid and free, respectively. The same procedure can be applied when joining elements to the grid, except that in this case, a node-to-zone link must be established between the node and the zone in which it lies. Node-to-node and node-to-zone linkage is controlled via the structure link command, and the linkage conditions are described in Structural-Element Links.
The element creation commands ( structure cable create
, structure beam create
, etc.) are designed to maintain a clear separation between different physical items being modeled. For example, if modeling two separate piles lying end-to-end, issue two separate structure pile create
commands and specify two separate IDs (e.g., 1 and 2). This will result in the creation of two nodes lying in the same geometric location: one is used by pile-1; one is used by pile-2. Forces and moments will not be transferred between the adjoining pile elements; instead, only forces will be transmitted into the surrounding zone at the common location. This mimics two separate piles lying end-to-end. If a single pile is desired, then issue two separate structure pile create
commands, but this time specify the same ID for each. This will result in the creation of a single node that is shared by the pile element on each side of the common location. Forces and moments will be transferred between the adjoining elements. In most modeling situations, the default link attachment conditions that are set by the element creation commands should not be modified, because these attachment conditions produce the desired element-grid interaction for each particular element type.
Specifying Boundary and Initial Conditions
All boundary and initial conditions (with the exception of distributed loads applied to beam and pile surfaces, pressure loads applied to shell, liner, and geogrid surfaces, and pretension forces applied to cables) are specified with the structure node command. The nodal conditions include
- velocity-fixity conditions,
- current velocity components, and
- applied point loads (forces and/or moments).
There are two coordinate systems associated with each node: the global system and the node-local system. The node-local system is used to specify attachment conditions that control how the node interacts with the grid. Also, the equations of motion are solved in these local directions. Therefore, one may fix or free velocities in these directions only. The orientation of the node-local system is set automatically at the start of a set of cycles based on the type of elements that use the node. (See the structure node command for a full description of these two systems.)
Velocities and rotations at nodes are fixed and freed in the node-local system using the structure node fix
and structure node free
commands. Velocities and rotations are initialized to specified values in the global system using the structure node initialize
command. Point loads are applied at nodes in either the global or the node-local system using the structure node apply
command.
Distributed loads are applied to elements using the structure cable apply
(for example). Linear elements (beam, cable, or pile) can apply distributed loads in the element local y and z directions. Planar elements (shell, geogrid, or liner) can apply pressure normal to the element surface. Note that in large-strain mode, the applied loads remain aligned with the corresponding element system directions, which may rotate as the element location changes.
Pretension forces are applied to cables using the structure cable apply tension
command. A positive pretension force places the cable into tension. See Pretensioning for additional information.
Stresses in Shells
This section provides a brief introduction to shell behavior. Much of the information in this section is taken from Cook et al. (1989). Consult that text for a more complete discussion.
A shell forms a curved surface in space. Usually a shell is thin in comparison with its span. Geometrically, a shell is described by its thickness, t, and the shape of the shell mid-surface. If the mid-surface is flat, then the shell is called a plate. In general, a shell simultaneously displays bending stresses and membrane stresses. Bending stresses in a shell correspond to bending stresses in a plate and produce bending and twisting moments and transverse-shear forces. Membrane stresses correspond to stresses in a plane-stress problem: they act tangent to the mid-surface, and produce mid-surface tangent forces. These moments and forces per unit length are called stress resultants. There are a total of eight stress resultants, which can be divided into those that arise from bending action and those that arise from membrane action. These will be described in the following two sections.
Bending Action
We can account for the bending action of a shell in terms of plate-bending theory, which extends beam theory from one dimension to two as follows. Define a surface coordinate system xyz such that x and y are orthogonal coordinates in the mid-surface and z is a direction normal to the mid-surface. Approximate the tangent plane to the shell mid-surface as a flat plate subjected to “plate bending,” meaning that external loads have no components parallel to the xy-plane and that \(σ_{xx}\) = \(σ_{yy}\) = \(σ_{xy}\) = 0 on the mid-surface z=0. Such a flat plate, like a straight beam, supports transverse loads by bending action. Figure 3 shows stresses that act on cross sections of a plate whose material is homogeneous and linearly elastic, subjected to plate-bending loading. Normal stresses \(σ_{xx}\) and \(σ_{yy}\) vary linearly with z, and are associated with bending moments Mx and My. Shear stress \(σ_{xy}\) also varies linearly with z, and is associated with twisting moment Mxy. Normal stress \(σ_{zz}\) is considered negligible in comparison with \(σ_{xx}\), \(σ_{yy}\) and \(σ_{xy}\). Transverse shear stresses \(σ_{yz}\) and \(σ_{xz}\) vary quadratically with z. Lateral load q includes surface load and body force, both in the z-direction.
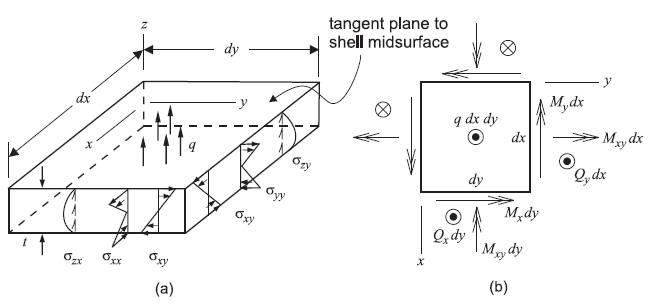
Figure 3: Bending action in a shell showing: (a) stresses that act on a differential element of a homogeneous, linearly elastic plate subjected to plate-bending loading; and (b) stress resultants corresponding with these stresses. (Stress resultants are drawn acting in their positive sense.)
Stresses in Figure 3 produce the bending stress resultants
and the transverse-shear stress resultants
The bending resultants are moments per unit length, and the transverse-shear resultants are forces per unit length. Differential total moments and forces are Mxdy, Qxdy, and so on, as shown in Figure 3. The following stress distributions are consistent with the assumptions of plate-bending theory, and satisfy (1) and (2):
Stresses \(σ_{xx}\), \(σ_{yy}\) and \(σ_{xy}\) are largest at the surface \(z = \pm t/2\), whereas transverse-shear stresses, \(σ_{xz}\) and \(σ_{yz}\), are largest at the mid-surface. Two points should be noted:
- The differential equations of equilibrium for a plate element under a general state of stress indicate that \(σ_{zz}\) varies as a cubic parabola over the thickness of the plate (Ugural 1981). But this stress, according to the assumptions of plate-bending theory, is negligible compared with the other stress components — this assumption becomes unreliable in the vicinity of highly concentrated transverse loads.
- \(σ_{xz}\) and \(σ_{yz}\), according to the assumptions of plate-bending theory, are negligible compared with the other stress components; however, when these stresses are integrated through the thickness, they produce transverse-shear stress resultants, Qx and Qy, that are of the same order of magnitude as the surface loading and moments.
Membrane Action
We can account for the membrane action of a shell in terms of plane-stress conditions. Define a surface coordinate system xyz such that x and y are orthogonal coordinates in the mid-surface, and z is a direction normal to the mid-surface. Approximate the tangent plane to the shell mid-surface as a flat plate subjected to plane-stress conditions, meaning that the plate is loaded in its own plane. Such a flat plate supports these loads by membrane action. Figure 4 shows stresses that act on cross sections of a plate whose material is homogeneous and linearly elastic, subjected to plane-stress loading. Normal and shear stresses \(σ_{xx}\), \(σ_{yy}\) and \(σ_{xy}\) are constant through the thickness.
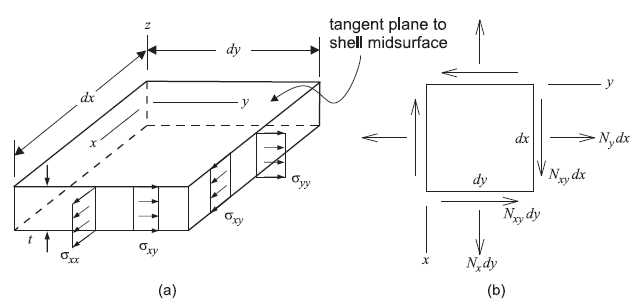
Figure 4: Membrane action in a shell showing: (a) stresses that act on a differential element of a homogeneous, linearly elastic plate subjected to plane-stress loading; and (b) stress resultants corresponding with these stresses. (Stress resultants are drawn acting in their positive sense.)
Stresses in Figure 4 produce the membrane stress resultants
The membrane resultants are forces per unit length. Differential total forces are Nxdy, Nydx and so on, as shown in Figure 4. The following stress distributions are consistent with the plane-stress assumptions and satisfy (4):
General Shell Stresses
A shell structure simultaneously displays bending stresses and membrane stresses. The stresses and stress resultants acting in a general shell consist of a superposition of these two loading modes (see Bending Action and Membrane Action). We can express these stress quantities in terms of a surface coordinate system xyz, where x and y are orthogonal coordinates in the shell mid-surface and z is a direction normal to the mid-surface. The eight stress resultants can be divided into bending (Mx, My, and Mxy), transverse-shear (Qx and Qy) and membrane (Nx, Ny and Nxy) stress resultants (see (1), (2), and (4)). The distribution of stress through the shell thickness follows from the particular plate or shell theory used to model structural behavior. For both the Kirchhoff (thin-shell) and Reissner (thick-shell) theories, the stress distributions correspond with a superposition of (3) and (5):
The stresses and stress resultants are sketched in Figure 3 and Figure 4, which also provide the sign convention for the stress resultants.
Stress Recovery Procedure
General shell stresses are computed in FLAC3D as follows. Refer to Stress Recovery Procedure for a more detailed description of the stress-recovery procedure. Each shell-type structural element (shell, geogrid, and liner) has an associated finite-element stiffness matrix that defines the structural response (see Finite Element Stiffness Matrices). Each shell-type element stores an internal force vector containing the generalized nodal forces acting on the element. During each timestep, the internal force vector is updated by multiplying the element stiffness matrix with the incremental nodal displacements (nodal velocities multiplied by timestep). Note that shell stresses are not computed during each timestep. Shell stresses are only computed by invoking a stress-recovery procedure that uses the internal force vector and the stiffness matrix to first compute stress resultants, and then compute stresses using (6). These stress resultants are in equilibrium with the generalized nodal forces acting on the element.
The structural properties of shell-type elements include material properties (e.g., \(E\) and \(\nu\) for an isotropic material) and thickness. These properties are embodied in the element stiffness matrix. If a structural property is modified during a simulation, then: (1) the generalized nodal forces and the stress resultants will remain the same; and (2) the stresses will change only if the thickness is altered (see (6) and note that a change in thickness will affect the stresses even if the stress resultants do not change).
Note that the same procedure is used for all shell-type structural elements, shell, geogrid, and liner. The command and FISH examples below use shell, but any of the shell-type keywords can be substituted.
The stress-recovery procedure requires that a consistent surface coordinate system be established prior to recovering any stress quantities. The surface coordinate system, xyz, establishes x and y as orthogonal coordinates in the shell mid-surface, and z as normal to the mid-surface. The stress resultants are expressed in terms of this system. The surface coordinate system is stored at each node, and can be set with the structure shell recover surface
command and the FISH function struct.node.system.surface
. It can be printed with the structure node list system-surface
command and plotted with the Shell, Geogrid, and Liner plot items.
After establishing the surface coordinate system over a patch of shell-type elements, stress resultants and stresses can be recovered for these elements with the structure shell recover resultants
and structure shell recover stress
commands. These values can be queried, sampled as histories, and viewed as colored contours:
- The values can be queried with the
structure shell list resultant
,structure shell list stress
, andstructure shell list stress-principal
commands, and the FISH functionsstruct.shell.resultant
,struct.shell.stress
, andstruct.shell.stress.prin
.- The values can be sampled as histories with the
structure shell history
command.- The values can be plotted as color contours with the Shell, Geogrid, or Liner plot item. Note that by default the plot items calculate an up-to-date value of the resultants and stresses, but they can be set to show the current engine values in the plot item attributes.
The stress resultants and stresses become invalid after any step is taken, or if the surface coordinate system is altered; also, the stresses become invalid if the depth factor is altered. In these cases, the values must be recovered again.
The stress-recovery procedure involves two steps: (1) creation of a consistent surface coordinate system; and (2) recovery of stress quantities. Both of these steps can be limited to only apply to a range of shell-type elements. This allows one to control whether nodal averaging will occur between shell-type elements that use the same node. For example, suppose that one wished to recover stresses throughout a capped cylindrical pressure vessel. The curvature across the cap edge is not continuous, and some of the stresses across this edge are also not continuous. We could recover stresses separately in the cap and in the cylinder walls by performing two separate recovery operations for the shell-type elements in these regions. When doing so, the z-direction of the surface coordinate system for the nodes along the edge would be different in each case.
Local Systems and Sign Conventions
Each element has its own local coordinate system. For beams and piles, this system is used to specify both the cross-sectional moments of inertia and applied distributed loading. For shells, geogrids and liners, this system is used to specify orthotropic material properties and applied pressure loading.
Each node has its own node-local coordinate system. This system is used to specify attachment conditions that control how the node interacts with the grid, and also defines the directions in which the equations of motion are solved. The orientation of the node-local system is set automatically at the start of a set of cycles based on the type of elements that use the node (see the structure node command).
Responses are computed for nodes and for each type of element. Nodal responses include forces and moments, as well as translational and rotational velocities and displacements. Forces and translational velocities are positive in the direction of the positive coordinate axes (either global or node-local) at the node. Positive moments and rotational velocities follow the “right-hand rule”: With the thumb pointing in the direction of the positive coordinate axis, the fingers are curled in the positive direction of rotation. The double arrows in Figure 3 indicate the direction of the right-hand thumb to define the positive moment and rotation.
Responses for each type of element, and the associated sign conventions, are described in the sections named “Response Quantities” associated with each element type (later in this chapter). The sign convention for force and moment distributions in beams and piles is shown in Beam Sign Conventions and Pile Sign Conventions, and the sign convention for stress resultants in shells, geogrids and liners is shown in Bending Action and Membrane Action, where the xyz-axes correspond with the surface coordinate system used during stress recovery (see Stress Recovery Proceture).
Specifying Damping and Timestep Conditions
The same damping conditions applied to the FLAC3D grid for static and dynamic analysis can also be applied to the structural elements. Note that the damping conditions specified with the zone mechanical damping
and zone dynamic damping
command only apply to the zones, and the structure damping
command must be used to specify damping conditions for the structural elements.
The structure damping
command can be used to change the damping condition, and the structure node damping-local
command can be used to change the damping constants at nodes for either local damping or combined damping. The timestep used for either static or dynamic analysis can be adjusted by using the structure safety-factor
command. Also, the computation of the rotational degree-of-freedom masses during dynamic analysis can be controlled by the structure scale-rotational-mass
command.
Thermal Expansion in Structural Elements
The effect of linear thermal expansion is implemented in the structural element formulation in FLAC3D. The temperature change occurs as a result of either heat conduction or temperature re-initialization in the FLAC3D zones (for model configure thermal
).
The effect of heat conduction in the structural element is not considered. It is assumed that the zone temperature is communicated instantaneously to the structural elements. The temperature change generates thermal expansion/contraction in the structural element axial direction. The effect of the lateral expansion in the element is neglected, and no other coupling takes place.
The incremental axial force generated by thermal expansion in the element is calculated using the formula (note that compression is positive for axial forces)
where E is the Young’s modulus of the element, A is the cross-sectional area, \(\alpha\) is the linear thermal expansion coefficient, and \(\Delta T\) is the temperature increment for the element.
The structural-element nodal temperature increment is determined by interpolation of nodal temperature increments in the host zone, and stored in a structural node offset. For a 1D structural element (i.e., beam, cable or pile), the temperature change is calculated as the average of values at the two nodes. The thermal strain increment of a 1D element is computed as the product of the thermal linear expansion coefficient, temperature change for the step, and element length. For a 2D structural element (i.e., shell, geogrid or liner), the temperature change is calculated as the average of values at the three nodes. The thermal strain increment of a 2D element is computed as the product of the thermal linear expansion coefficient, temperature change for the step, and the lengths of the vectors from the element centroid to each node. (There are three of these vectors.) Thermal strains, thermal strain increments and temperatures at structural nodes are not stored.
Note that when a large temperature increment is specified for cables, it is advisable to assign nonzero compressive yield strength to the cables in order to avoid compressive yielding during the thermal expansion stage.
Material Properties
Properties are assigned to structural elements with the structure shell property
command (or the equivalent for beam, cable, pile, geogrid, or liner elements). The range logic can be used to limit the property settings to only those elements within the specified range. The properties for each structural-element type are described in detail in the following sections. Note that all quantities must be given in a consistent set of units as shown in the table below.
Property | Unit | SI | Imperial | ||||
---|---|---|---|---|---|---|---|
area | length2 | m2 | m2 | m2 | cm2 | ft2 | in2 |
axial or shear stiffness | force/disp | N/m | kN/m | MN/m | Mdynes/cm | lbf /ft | lbf/in |
exposed perimeter | length | m | m | m | cm | ft | in |
moment of inertia | length4 | m4 | m4 | m4 | cm4 | ft4 | in4 |
plastic moment | force-length | N-m | kN-m | MN-m | Mdynes-cm | ft-lbf | in-lbf |
yield strength | force | N | kN | MN | Mdynes | lbf | lbf |
Young’s modulus | stress | Pa | kPa | MPa | bar | lbf /ft2 | psi |
where, 1 bar = 106 dynes/cm2 = 105 N/m2 = 105 Pa.
Nodes & Links: Connection to the Grid
The following topics describe nodes and links.
Type-Specific Information
The following sections detail each type of structural element.
General Commands & FISH
Was this helpful? ... | PFC 6.0 © 2019, Itasca | Updated: Nov 19, 2021 |