FLAC3D Theory and Background • Constitutive Models
Concrete Model
This concrete model is a plastic-damage model extended and modified from the work in Lublinear et al (1989) and Lee & Fenves (1998) using the concepts of fracture-energy-based damage and modulus degradation in continuum damage mechanics.
Formulations
Modulus Degradation
Based on the concept of the continuum damage theory , the stress σ is linked with the effective stress ˉσ [note: in this model, the concept of “effective stress” is a concept in damage theory, which is different from the concept of Terzaghi’s effective stress in fluid-machinal interaction. A variable with a bar on top is in terms of effective stress] by an isotropic damage factor D:
(1)σij=(1−D)ˉσij
together with Hookie’s law ˉσij=Eijklϵekl and additive strain decomposition ϵij=ϵeij+ϵpij, it obtains that
(2)σij=(1−D)ˉσij=(1−D)Eijkl(ϵkl−ϵpkl)
In other words, the nominal elastic modulus is in degradation by a factor of (1−D) from the elastic modulus if relating nominal stress σ and strain ϵ: E→(1−D)E.
Damage Based on Fracture-Energy
In this model, two damage variables, one for tensile damage and the other for compressive damage, are defined independently, and each variable is factorized into the effective-stress response and stiffness degradation response parts. Considering a uniaxial tensile or compressive stress state, the state variable χ∈[c,t] is introduced. The state is uniaxial tensile for χ=t and uniaxial compressive for χ=c.
The stress is assumed to be determined by the plastic strain. The relation between the uniaxial stress, denoted by σχ, and the corresponding scalar plastic strain, denoted by ϵpχ, is assumed as
(3)σχ=fχ0[(1+aχ)exp(−bχϵpχ)−aχexp(−2bχϵpχ)]
where aχ and bχ are positive material constants to be determined, and fχ0 is the initial yield stress without damage.
Suppose that we have available experimentally derived stress-strain diagrams in uniaxial tension and compression (top ones in Figure 1 & 2), and that these can be converted into σχ-ϵpχ curves (bottom ones in Figure 1 & 2). Assume that the area under these curves are infinite and equal to gχ, define
(4)κχ=1gχ∫ϵpχ0σχdϵpχ
where apparently 0≤κχ≤1. Stress in terms of ϵpχ, or σχ=f(ϵpχ), can rewritten (Lublinear et al, 1989) in terms of κχ, or
(5)σχ=f(κχ)=fχ0aχ[(1+aχ)√ϕ(κχ)−ϕ(κχ)]
where ϕ(κχ)=1+aχ(2+aχ)κχ.
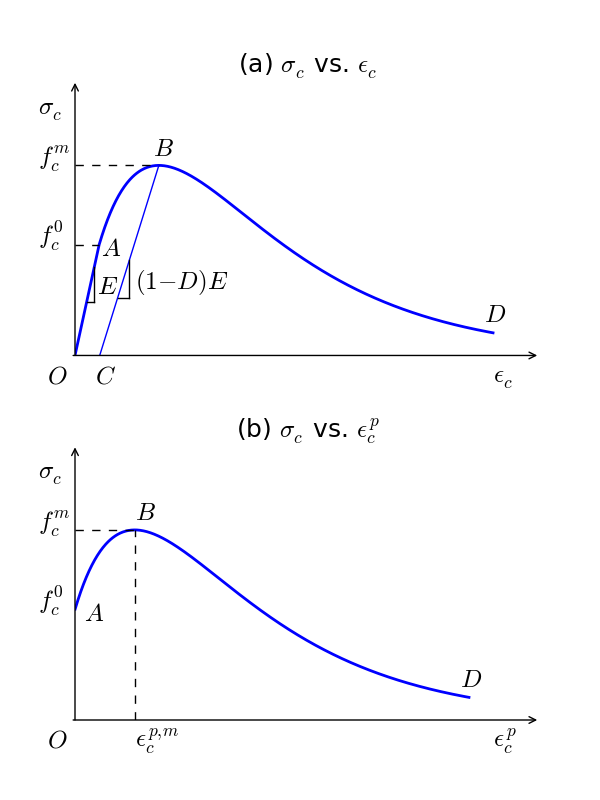
Figure 1: Typical uniaxial compression curves: top - uniaxial compressive stress vs compressive strain; bottom - uniaxial compressive stress vs plastic compressive strain.
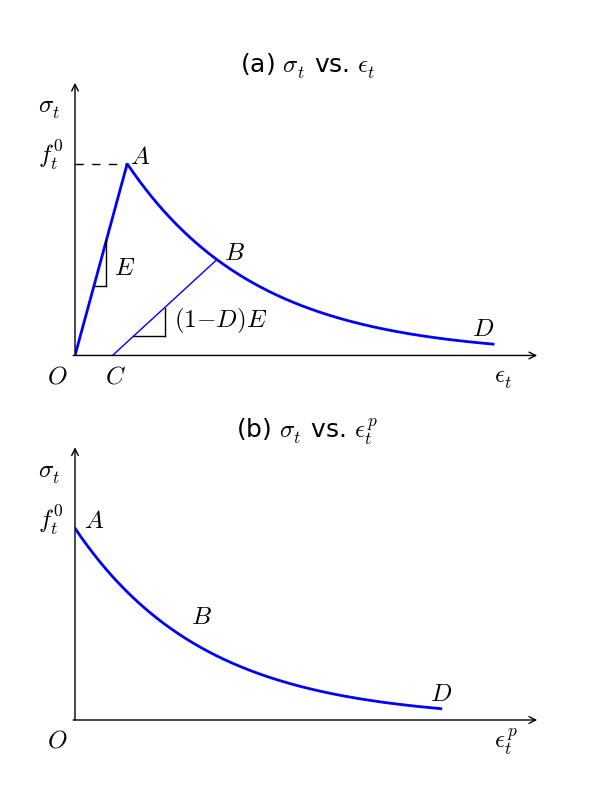
Figure 2: Typical uniaxial tension curves: top - uniaxial tensile stress vs tensile strain; bottom - uniaxial tensile stress vs plastic tensile strain.
For stress defined by Equation (3), the quantity gχ, which denotes the dissipated energy density during the entire process of microcracking, has a closed-form expression of the area under the curve of A-B-D in Figure 1-(b) or 2-(b):
(6)gχ=∫+∞0σχdϵpχ=fχ0bχ(1+aχ2)
The initial slope of the curve σχ-ϵpχ is
(7)dσχdϵpχ|ϵpχ=0=fχ0bχ(aχ−1)
Note that aχ>1 implies initial hardening (e.g., when χ=c) and aχ<1 implies softening immediately after yielding (e.g., when χ=t). When aχ>1, σχ obtain a maximum value (see Point A in Figure 1)
(8)fmχ=fχ0(1+aχ)24aχ
at
(9)ϵp,mχ=−ln(1+aχ2aχ)bχ
For a curve with initial hardening after yielding which is typical in uniaxial compression, the material constant aχ can be back-calculated from Equation (8) by
(10)aχ=2(fmχ/fχ0)−1+2√(fmχ/fχ0)2−(fmχ/fχ0)
For a curve with immediate softening after yielding which is typical in uniaxial extension, a simple way is assuming at=0, which leads to
(11)σt=ft0exp(−btϵpt)
and
(12)gt=ft0/bt
Once aχ is determined or assumed, bχ can be obtained from Equation (6) provided gχ and fχ0 are known.
Because the capacity for the dissipated energy per unit volume cannot be given as a material property, gχ should be derived from other known material properties such as the fracture energy (Lee & Fenvas, 1998). Assuming that the fracture energy in the uniaxial tensile state Gχ and its counterpart in the uniaxial compressive state are given as a material properties, gχ is the specific fracture energy normalized by the localization zone size, also referred to as the characteristic length lχ, which leads to (Lubliner et al. 1989)
(13)gχ=Gχlχ
To maintain objective results at the structural level, lχ should be an objective value or assumed as a material property.
Yield Function
The yield surface is schemed by Figure Figure #model-concrete-yd
in the biaxial-stress (plane-stress) space. Note that we assume the principle stresses with the order σ1≤σ2≤σ3 and positive for tension. Due to symmetry, only A-B-C-D is considered.
For line A-B, a tension yield criteria is used:
(14)ft(ˉσ)=ˉσ3−ˉσt=0
For line B-C, a Mohr-Coulomb yield criteria is used:
(15)fs(ˉσ)=−ˉσtˉσ1+ˉσcˉσ3−ˉσcˉσt=0
For curve C-D, a Drucker-Prager yield criteria is used:
(16)fd(ˉσ)=αˉI1+ˉq−(1−α)ˉσc=0
where ˉI1 is the first stress invariant, ˉq is the equivalent shear stress, and
(17)α=fb0/fc0−12(fb0/fc0)−1
where fc0 is the uniaxial yield compressive strength and fb0 is the biaxial yield compressive strength. Since usually fb0≥fc0, α is in the range of 0≤α<0.5.
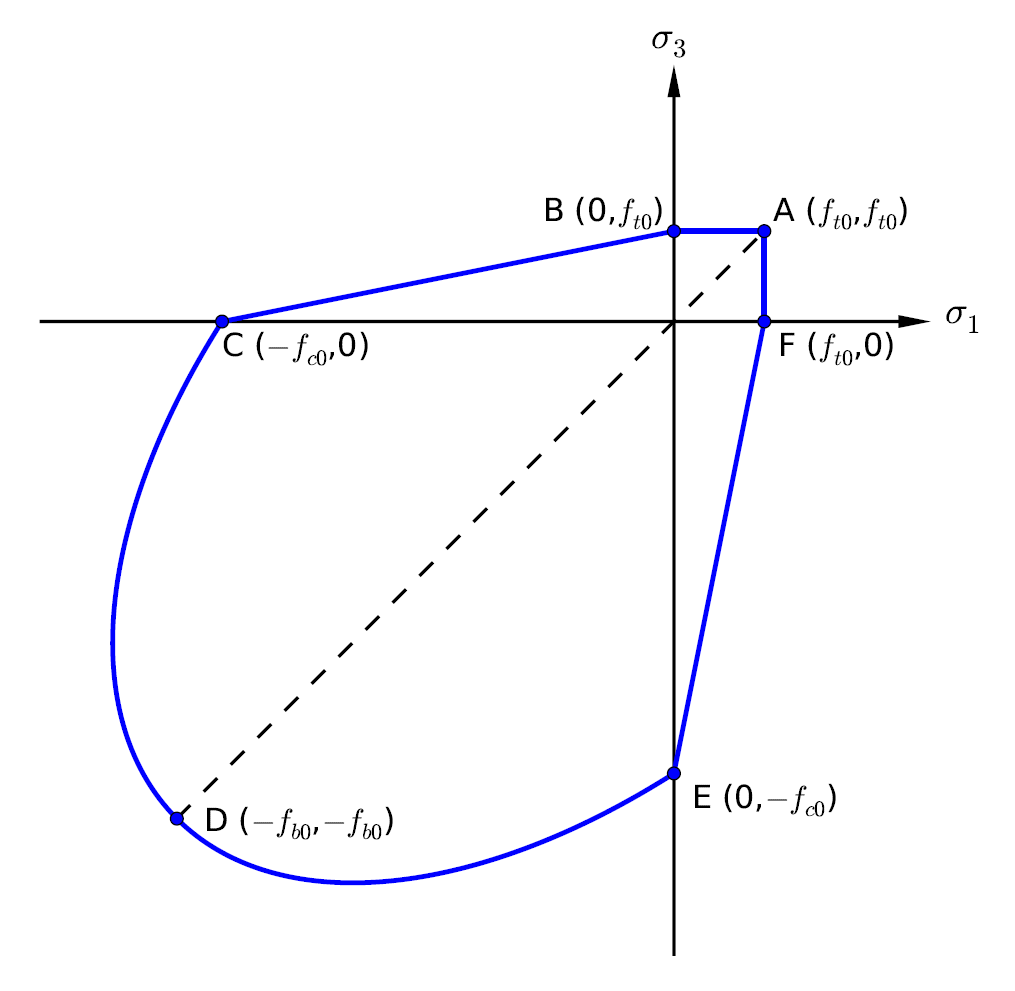
Figure 3: Schematic of initial yield surface in the biaxial-stress (plane-stress) space.
Flow Rule
The plastic strain rate is evaluated by the flow rule, which is defined by a scalar plastic potential function g. For a plastic potential in the effective stress space, the plastic strain is given by
(18)Δϵpij=λ∂g∂ˉσij
where λ is a non-negative function referred to as the plastic consistency parameter (plastic multiplier).
For yielding at line A-B, an associated potential function is used:
(19)gt(ˉσ)=ˉσ3−ˉσt
For yielding at line B-C, a nonassociated Mohr-Coulomb type potential function is used:
(20)gs(ˉσ)=−ˉσ1+Nψˉσ3
where Npsi=min(ˉσc/ˉσt,(1+sinψ)/(1−sinψ) and ψ is the dilation angle which is an input material property.
For yielding at curve C-D, a nonassociated Drucker-Prager yield criteria is used:
(21)gd(ˉσ)=αpˉI1+ˉq
where αp=min(α,6sinψ/(3−sinψ)).
Another internal variable set, besides the plastic strain, is needed to represent the damage states. The damage variable, κχ, is assumed to be the only necessary state variable and its evolution is expressed as
(22)Δκt=r(ˉσ)ftgtΔϵp3(23)Δκc=(1−r(ˉσ))fcgcΔϵp1
where ϵp1 is the minimum principal plastic strain, ϵp3 is the maximum principal plastic strain; r is a weight function of the effective principal stresses, which ranges from 0 in pure compressive loading to 1 in pure tensile loading:
(24)r(ˉσ)=∑3i=1⟨ˉσi⟩∑3i=1|ˉσi|
Evolution of Damage
To model the different damage states for tensile and compressive loading, both κt and κc are used as independent damage variables. The evolution equations for the hardening and degradation variables are obtained from the factorization of the uniaxial stress strength function, fχ=fχ(κχ), such that
(25)fχ=(1−Dχ)ˉfχ
in which 0≤Dχ<1 and ΔDχ>0. ˉσχ=ˉfχ describes the evolution of the cohesion variable used in the yield function, and Dχ=Dχ(κχ) defines the degradation damage as a function of the damage variable:
(26)D=1−(1−Dc)(1−sDt)
where
(27)s=s0+(1−s0)r(ˉσ)
with 0≤s0≤1 and so s0≤s≤1 represents stiffness recovery.
The degradation is also assumed an exponent form as
(28)1−Dχ=exp(−dχϵpχ)
where dχ are material constants, which can be determined form the unloading-reloading (see B-C lines in Figure 1-a & 2-a).
Material Properties
In this model, two material properties, initial Young’ modulus and Poisson’s ratio, (E, ν), or initial bulk and shear modulus, (K, G), are required to determine the elasticity.
To match the uniaxial compression and tension experimental curves, one straightforward approach is to specify the initial and peak (maximum) strengths (fχ0 and fmχ), fracture energies (Gχ), characteristic lengths (lχ), and damages at specific stresses (Dpeakc and Dhalft) in the uniaxial compression/tension states. These input will determine the parameters aχ, bχ, dχ and gχ.
Once fχ0 and fmχ are known, there are two cases:
if the curve is hardening and then softening (usually in uniaxial compression experiments, see Figure 1), or in other words, fmχ>fχ0, then aχ can be determined by Equation (10).
if the curve is immediately softening (usually in uniaxial extension experiments, see Figure 2), or in other words, fmχ=fχ0, then aχ will be assumed zero.
Once Gχ and lχ are known, then gχ=Gχ/lχ, bχ can then be determined by Equation (6) so that bχ=fχ0(1+aχ/2)/gχ.
Equation (28) can determine dχ:
for uniaxial compression where the curve is hardening and then softening, then dc can be calculated by the the damage at the peak stress,
(29)dc=bcln(1−Dpeakc)ln(1+ac2ac)
for uniaxial extension where the curve is immediately softening, then dt can be calculated by the the damage at the half peak/initial stress,
(30)dt=btln(1−Dhalft)−ln2
αp is a material property determining the dilation, with typical value αp=0.2.
The biaxial compression initial strength fb0 is requited to calculate α in Equation (17). Here the ratio fb0/fc0 is instead as an input material property, with a typical value fb0/fc0=1.05∼1.2.
The stiffness recovery parameter s0 is usually in the range of 0≤s0≤0.2.
References
Lee, J., & Fenves, G. L. (1998). Plastic-damage model for cyclic loading of concrete structures. Journal of engineering mechanics, 124(8), 892-900.
Lee, J., & Fenves, G. L. (1998). A plastic damage concrete model for earthquake analysis of dams. Earthquake engineering & structural dynamics, 27(9), 937-956.
Lubliner, J., Oliver, J., Oller, S., & Onate, E. (1989). A plastic-damage model for concrete. International Journal of solids and structures, 25(3), 299-326.
concrete Model Properties
Use the following keywords with the zone property
command to set these properties of the concrete model.
- bulk f
bulk modulus, K.
- compression-strength f
uniaxial compression peak/maximum strength, fmc.
- compression-initial f
uniaxial compression initial yield strength, fc0.
- compression-energy-fracture f
fracture energy in uniaxial compression state, Gc.
- compression-length-reference f
reference (characteristic) length in uniaxial compression state, lc.
- compression-d f
compression damage parameter, dc.
- dilation f
dilation angle, ψ.
- poisson f
Poisson’s ratio, ν.
- ratio-biaxial f
strength ratio of biaxial to uniaxial compression initial, usually in a range of (1,1.25], fb0/fc0.
- shear f
shear modulus, G.
- tension-strength f
uniaxial tension peak/maximum strength, fmt.
- tension-initial f
uniaxial tension initial yield strength, ft0. Usually, ft0=fmt.
- tension-energy-fracture f
fracture energy in uniaxial compression state, Gt.
- tension-length-reference f
reference (characteristic) length in uniaxial tension state, lt.
- tension-d f
tension damage parameter, dt.
- tension-recovery f
stiffness recovery parameter for tension, typical value is 0.2, s0.
- young f
Young’s modulus, E.
- compression f (r)
Current compression strength, σc.
- damage f (r)
Current total damage, D.
- damage-compression f (r)
Current damage in compression, Dc.
- damage-tension f (r)
Current damage in tension, Dt.
- strain-plastic-compression f (r)
Current plastic strain in compression, ϵpc.
- strain-plastic-tension f (r)
Current plastic strain in tension, ϵpt.
- tension f (r)
Current tension strength, σt.
Notes
Only one of the two options is required to define the elasticity: bulk modulus K and shear modulus G, or, Young’s modulus E and Poisson’s ratio ν. When choosing the latter, Young’s modulus E must be assigned in advance of Poisson’s ratio ν.
Key
- (a) Advanced property.
This property has a default value; simpler applications of the model do not need to provide a value for it.
- (r) Read-only property.
This property cannot be set by the user. Instead, it can be listed, plotted, or accessed through FISH.
Was this helpful? ... | Itasca Software © 2024, Itasca | Updated: Apr 15, 2025 |