Burgers-Mohr/Power-Mohr Model: Loading/Unloading Compression Test
Note
To view this project in 3DEC, use the menu command . The project’s main data files are shown at the end of this example.
This example shows the influence of loading rate on the axial stress response of a viscoplastic sample in an unconfined compression test. The viscoelastic behavior of the sample obeys a generalized Kelvin law. Yielding is characterized by a Mohr-Coulomb failure criterion in both cases. The viscoplastic behavior is compared to that of a second sample, made of elasto-plastic Mohr-Coulomb material, and undergoing the same velocity-controlled compression test. All values quoted in this section may be interpreted in any consistent system of units, but are probably not representative, and are given only for purposes of illustration.
The viscoplastic and viscoelastic samples are represented by one brick each, using the Burgers-Mohr model, and the Mohr-Coulomb model. To represent the generalized Kelvin viscous behavior, the viscous component of the Maxwell cell in viscosity-maxwell is not activated. In the first part of the test, a vertical compressive velocity of magnitude 10-4 (in units of distance per unit time) is applied on both sides of the samples for a total of 1500 steps. The timestep is set to 10-3, a value small compared to the ratio ηK/GK of 10.
For the unconfined compression test considered here, the Mohr-Coulomb failure criterion predicts that shear yielding will take place when the axial stress reaches the value of −2C√Nϕ (≃−1.28 × 106). On the other hand, the axial stress in the elasto-plastic sample is given, up to incipient failure, by the elastic relation
where α1=K+4/3G, α2=K−2/3G, ϵxx=−2vt/L, v is the applied velocity magnitude, t is the simulation time elapsed to incipient failure, and L is the horizontal length of the sample.
The numerical results are presented in Figure 1. Note that the Burgers-Mohr sample fails at the same stress level, but later in time, thus reflecting the effect of creep (at incipient failure, for the model parameter used in the simulation, the time is about 1.00 for the Burgers-Mohr sample). When the loading rate is increased, and the simulation is repeated for the same final amount of deformation (the applied velocity is increased, the same number of steps is used but the timestep is reduced), the responses of the two models become more similar. For a velocity of 10-2, the effect of creep cannot be detected on the plot—see Figure 2 (at incipient failure, the creep time is now about 0.75 × 10-2).
In the second part of the test, the compressive velocity is set to zero and the models are cycled for 500 steps. While the Mohr-Coulomb sample stays at yield, the Burgers-Mohr sample unloads as creep develops (see Figure 3). The interaction between creep and plastic flow in the Burgers-Mohr sample may be appreciated by comparing the viscoplastic behavior in Figure 3 and Figure 4; in the latest plot, more plastic flow (measured by strain-shear-plastic) is allowed to take place before the compressive velocity is set to zero and, subsequently, the magnitude of maximum creep unloading is reduced.
In the third part of the test, the samples are “reloaded” by application of a 3DEC velocity of 5 × 10-5, for a total of 2000 steps. At this stage, both samples are yielding at the same stress level (see Figure 5). To complete the test, the compressive velocity is set to zero again and the models are cycled for another 1500 steps. The evolution of axial stress during this final stage may be observed in Figure 5.
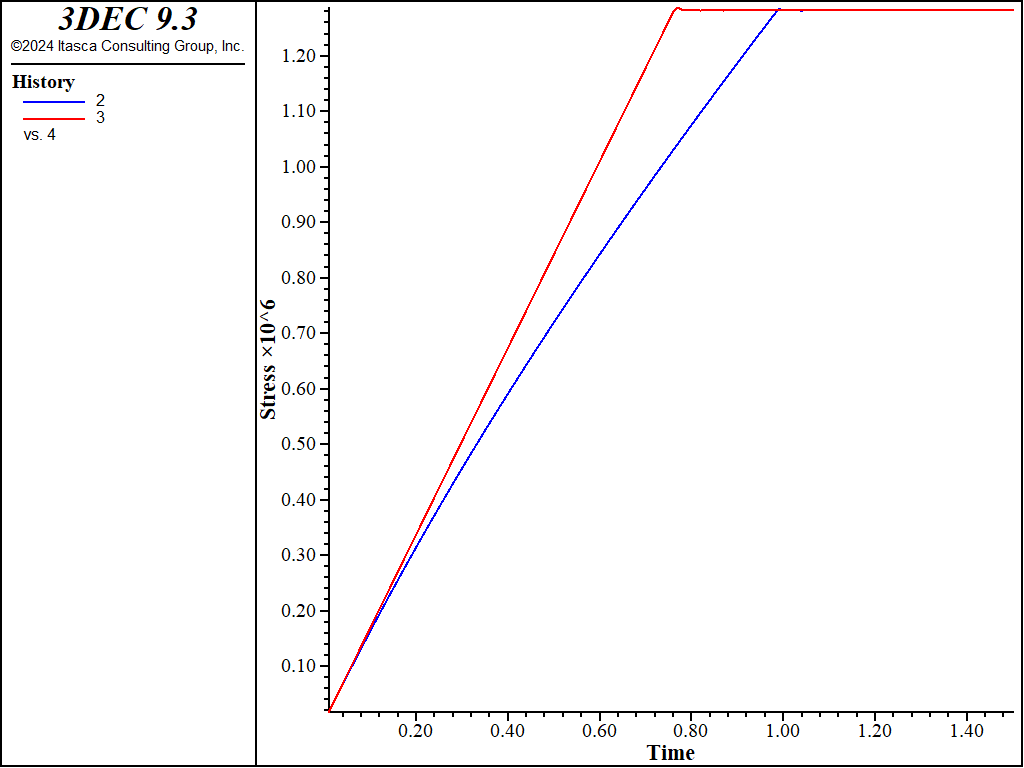
Figure 1: Axial stress versus time for slow compression test—Burgers-Mohr and Mohr-Coulomb models.
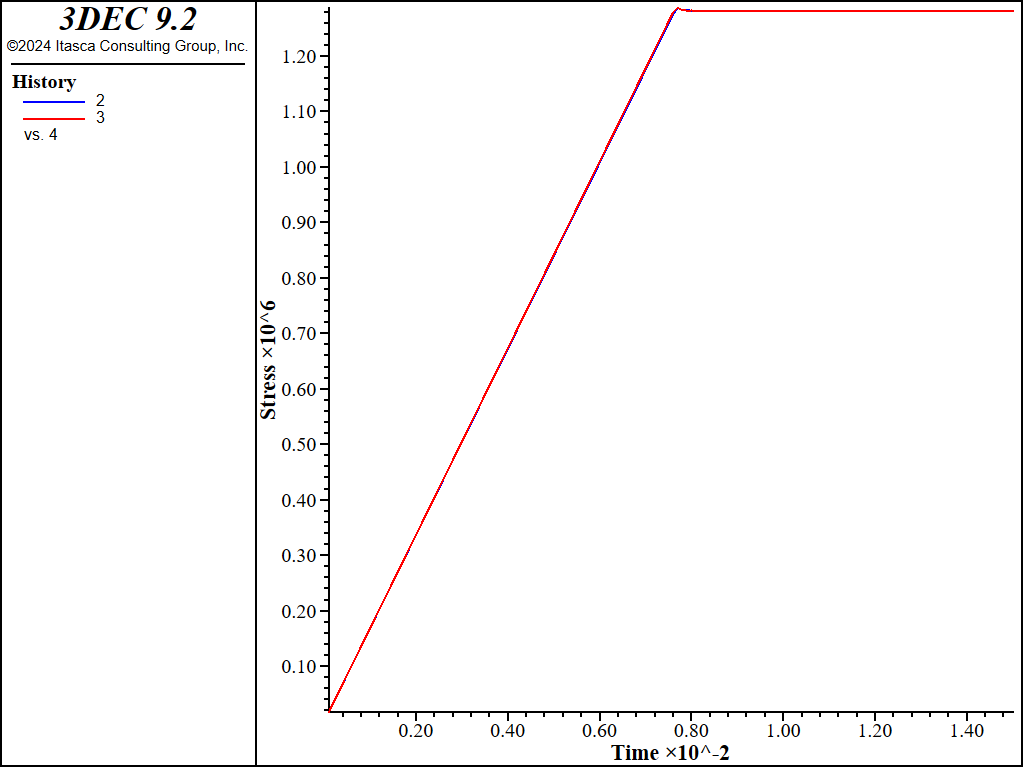
Figure 2: Axial stress versus time for rapid compression test—Burgers-Mohr and Mohr-Coulomb models.
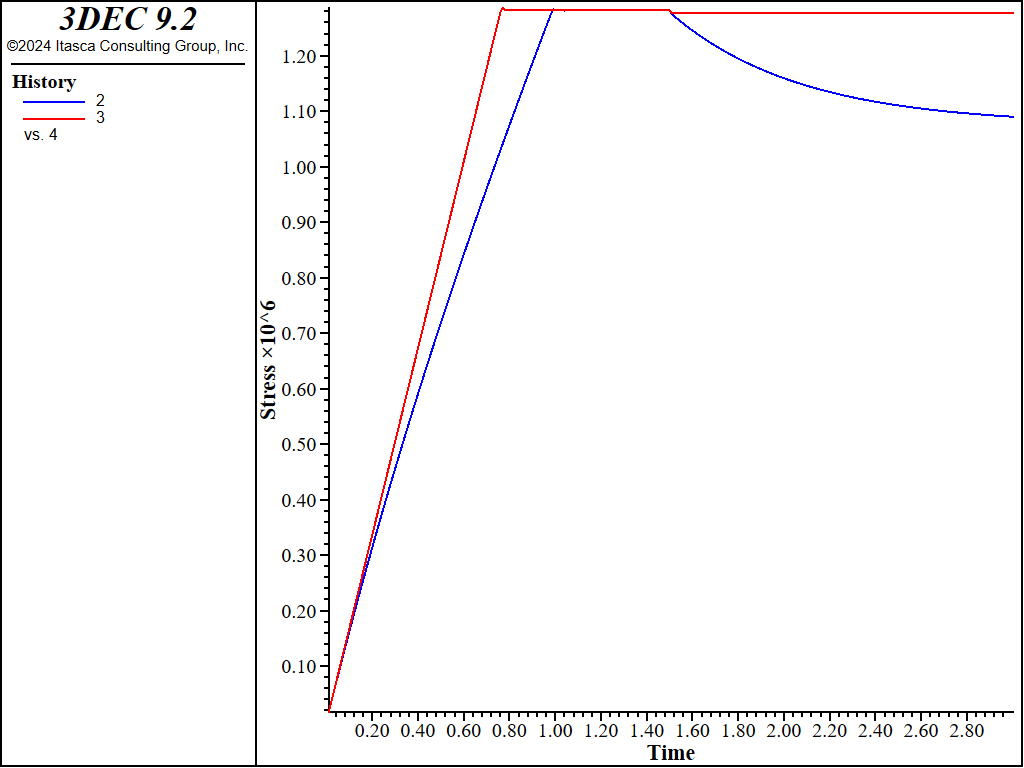
Figure 3: Creep unloading after less plastic flow—Burgers-Mohr and Mohr-Coulomb models.
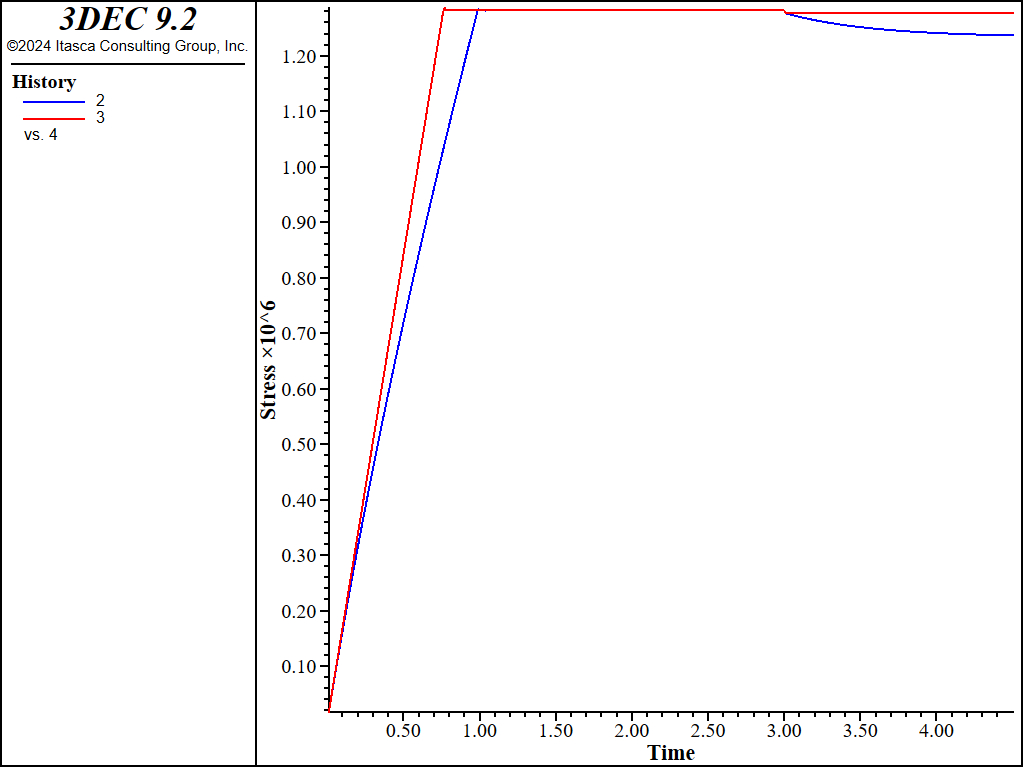
Figure 4: Creep unloading after more plastic flow—Burgers-Mohr and Mohr-Coulomb models.
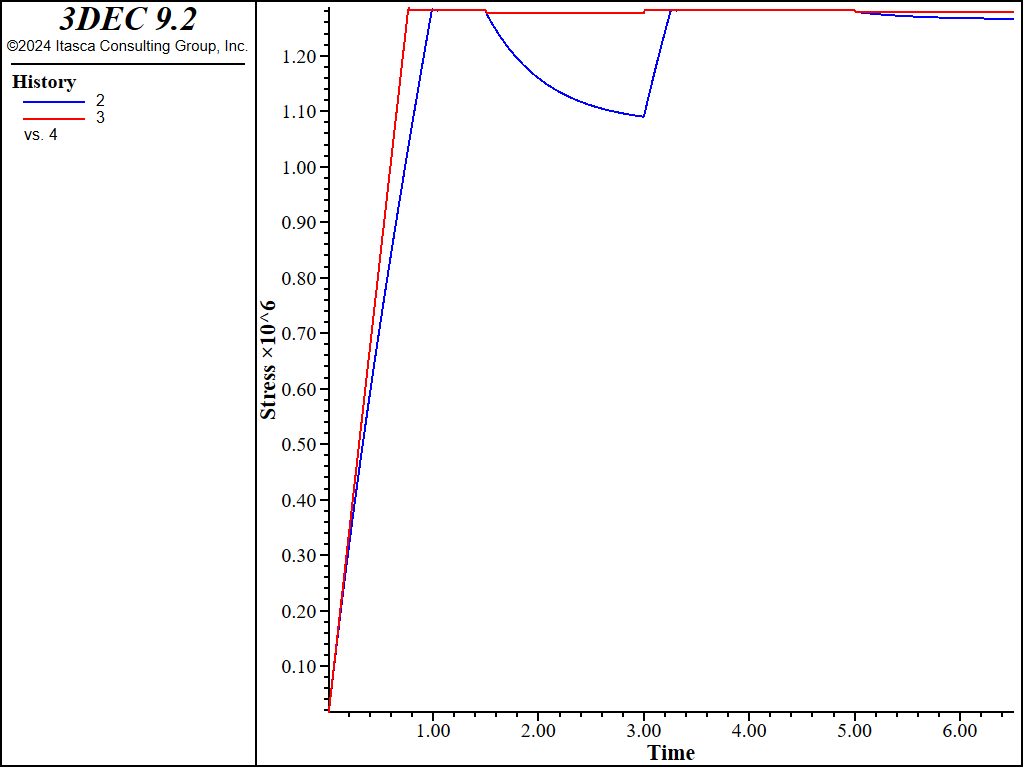
Figure 5: Axial stress versus time for several loading excursions—Burgers-Mohr, Power-Mohr, and Mohr-Coulomb models.
Data Files
CompressionBurgers.dat
model new
;File: CompressionBurgers.dat (formerly example 1.6.7)
;Title:Compression test on Burger-creep viscoplastic and Mohr material
;
model configure creep
model large-strain off
block create brick 0 3 0 1 0 1
block create brick 6 9 0 1 0 1
block zone generate edgelength 10
block zone group 'mo'
block zone group 'cv' range position-x 0 3
block zone cmodel assign mohr-coulomb range group 'mo'
block zone property density 2.5E3 bulk 1.19E10 shear 1.1E10 friction 44 ...
cohesion 2.72E5 tension 2E5 range group 'mo'
block zone cmodel assign burgers-mohr range group 'cv'
block zone property density 2.5E3 bulk 1.19E10 shear-kelvin 1.1E10 ...
shear-maxwell 1.1E10 viscosity-kelvin 1.1E10 ...
cohesion 2.72E5 friction 44 tension 2E5 range group 'cv'
; --- fish functions ---
program call 'compression.fis'
[squez(1.0e-4)]
block history displacement-x position 0.0 0.0 0.0
fish history CVisc
fish history Mohr
model history creep time-total
model save 'compression_test_ini'
;
model restore 'compression_test_ini'
model creep timestep starting 0.0010
model creep timestep fix 0.0010
model cycle 1500
model title 'Slow Compression Test'
model save 'compression_test_slow'
;
model restore 'compression_test_ini'
model creep timestep starting 1e-5
model creep timestep fix 1e-5
[squez(1e-2)]
model cycle 1500
model title 'Rapid Compression Test'
model save 'compression_test_fast'
;
model restore 'compression_test_ini'
model creep timestep starting 1e-3
model creep timestep fix 1e-3
model cycle 1500
[squez(0)]
model cycle 1500
model title 'Less Plastic Flow'
model save 'compression_test_lessflow'
;
model restore 'compression_test_ini'
model creep timestep starting 1e-3
model creep timestep fix 1e-3
model cycle 3000
[squez(0)]
model cycle 1500
model title 'More Plastic Flow'
model save 'compression_test_moreflow'
;
model restore 'compression_test_ini'
model creep timestep starting 1e-3
model creep timestep fix 1e-3
model cycle 1500
[squez(0)]
model cycle 1500
;
[squez(5.0e-5)]
model cycle 2000
;
[squez(0)]
model cycle 1500
model title 'Several Load Cycles'
model save 'compression_test_cycles'
program return
⇐ WIPP-Salt Model: Shear Compression Test | WIPP-Drucker Model: Compression Test Showing Localization ⇒
Was this helpful? ... | Itasca Software © 2024, Itasca | Updated: Dec 05, 2024 |