Lined Circular Tunnel in an Elastic Medium with Anisotropic Stresses
Problem Statement
Note
To view this project in FLAC2D, use the menu command . The main data file used is shown at the end of this example. The remaining data files can be found in the project.
A circular tunnel with a radius of 5 m is located at 30 m depth in a soft elastic soil. The in-situ stresses are 600 kPa vertical and 300 kPa horizontal. The tunnel is supported by a 125 mm thick shotcrete liner. The support is installed simultaneously with the excavation in a preexisting anisotropic biaxial stress field. The support displacements and stress resultants (in terms of thrust and moment), and the coupling contact stresses are computed under plane-strain conditions for the two limiting conditions of no-slip (no relative shear displacement) and full-slip (no shear stress transmission) at the ground-support coupling. These computed values are compared with the analytical solution of Einstein and Schwartz (1979).
Analytical Solution
The analytical solution (Einstein and Schwartz 1979) is expressed using the notation in Figure 1. The support displacements consist of a radial, \(u_s\), and a tangential, \(v_s\), component. The internal stresses consist of a circumferential thrust, \(T\), and a bending moment, \(M\). The coupling contact stresses consist of a normal, \(\sigma_R\), and a shear, \(\tau_{R\theta}\), component.
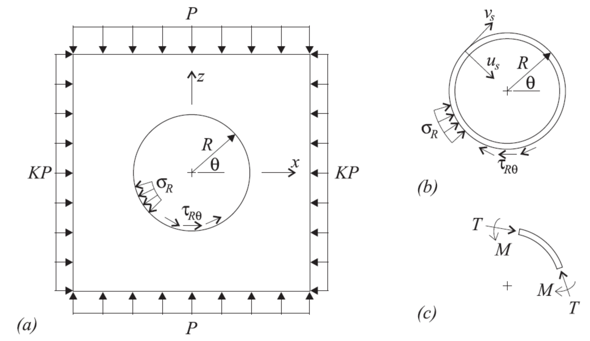
Figure 1: Notation for analytical solution: (a) ground medium; (b) tunnel liner; and (c) positive sense of internal stress resultants in liner.
No-Slip Solution — For the no-slip solution, the coupling boundary condition consists of no relative shear displacement between the ground and the support. The no-slip solution is given in the following equations:
where: |
\(\theta\) |
= |
angular location (counterclockwise with respect to horizontal); |
\(R\) |
= |
tunnel radius; |
|
\(P\) |
= |
vertical stress; |
|
\(K\) |
= |
ratio of horizontal-to-vertical stress; |
|
\(E\) |
= |
Young’s modulus of the ground mass; |
|
\(\nu\) |
= |
Poisson’s ratio of the ground mass; and |
|
\(a^*_0,a^*_2,b^*_2\) |
= |
dimensionless coefficients (see the next equations below). |
where: |
\(C^*\), \(F^*\) |
= |
compressibility and flexibility ratios, respectively (see the next two equations). |
where: |
\(E_s\) |
= |
Young’s modulus of the support; |
\(\nu_s\) |
= |
Poisson’s ratio of the support; |
|
\(A_s\) |
= |
average cross-sectional area of support per unit length of tunnel |
|
(for support of constant thickness \(t\), \(A_s = t\)); and |
|||
\(I_s\) |
= |
moment of inertia of support per unit length of tunnel |
|
(for support of constant thickness \(t\), \(I_s = t^3/12\)). |
Full-Slip Solution — For the full-slip solution, the coupling boundary condition consists of no shear stress transmission between the ground and the support. The full-slip solution is given in the following equations:
where: |
\(\theta\) |
= |
angular location (counterclockwise with respect to horizontal); |
\(R\) |
= |
tunnel radius; |
|
\(P\) |
= |
vertical stress; |
|
\(K\) |
= |
ratio of horizontal-to-vertical stress; |
|
\(E\) |
= |
Young’s modulus of the ground mass; |
|
\(\nu\) |
= |
Poisson’s ratio of the ground mass; and |
|
\(a^*_0\), \(a^*_2\) |
= |
dimensionless coefficients (see the next equations). |
where: |
\(C^*\), \(F^*\) |
= |
compressibility and flexibility ratios, respectively (see equation (1) above). |
FLAC2D Model
The problem is described in terms of the following parameters from the analytical solution:
Geometry |
|
tunnel radius (\(R\)) |
5 m |
In-Situ Stresses |
|
vertical stress (\(P\)) |
600 kPa |
ratio of horizontal-to-vertical stress (\(K\)) |
0.5 |
(\(\sigma_{xx}=-300\) kPa; \(\sigma_{yy}=-600\) kPa) |
|
Ground Mass Properties |
|
Young’s modulus (\(E\)) |
48 MPa |
Poisson’s ratio (\(\nu\)) |
0.34 |
(shear modulus = 17.91 MPa; bulk modulus = 50 MPa) |
|
Liner Properties |
|
Young’s modulus (\(E_s\)) |
25 GPa |
Poisson’s ratio (\(\nu_s\)) |
0.15 |
thickness (\(t\)) |
125 mm |
The FLAC2D model simulates a thin slice of a circular tunnel in an infinite elastic ground mass with a preexisting anisotropic biaxial stress field subjected to plane-strain conditions. The far-field boundaries are placed at a distance of 20 times the tunnel radius to approximate infinite boundaries. The in-situ stresses are installed in all zones and also applied as loads acting on the far-field boundaries. Symmetry boundary conditions are also imposed on the planes at \(x=0\) and \(y=0\). For gridpoints, this requires maintaining zero displacement normal to the plane. For nodes, this requires maintaining zero displacement normal to the plane and zero rotation in the plane. (The appropriate nodal conditions are imposed by realigning and then fixing the appropriate node-local systems, and also specifying the proper velocity-fixity conditions.
The FLAC2D grid is graded as one moves away from the tunnel (see Figure 2). The model resolution is 24 zones along the tunnel boundary. Liner structural elements are attached to the zone faces lying along the tunnel boundary (see Figure 3). The liner-zone coupling stiffnesses (\(k_n\) and \(k_s\)) are chosen using the liner-stiffness equation, and increasing the value by a factor of 100 as suggested in the text following this equation. We will confirm below that the criterion of small coupling deformation is met for our system.
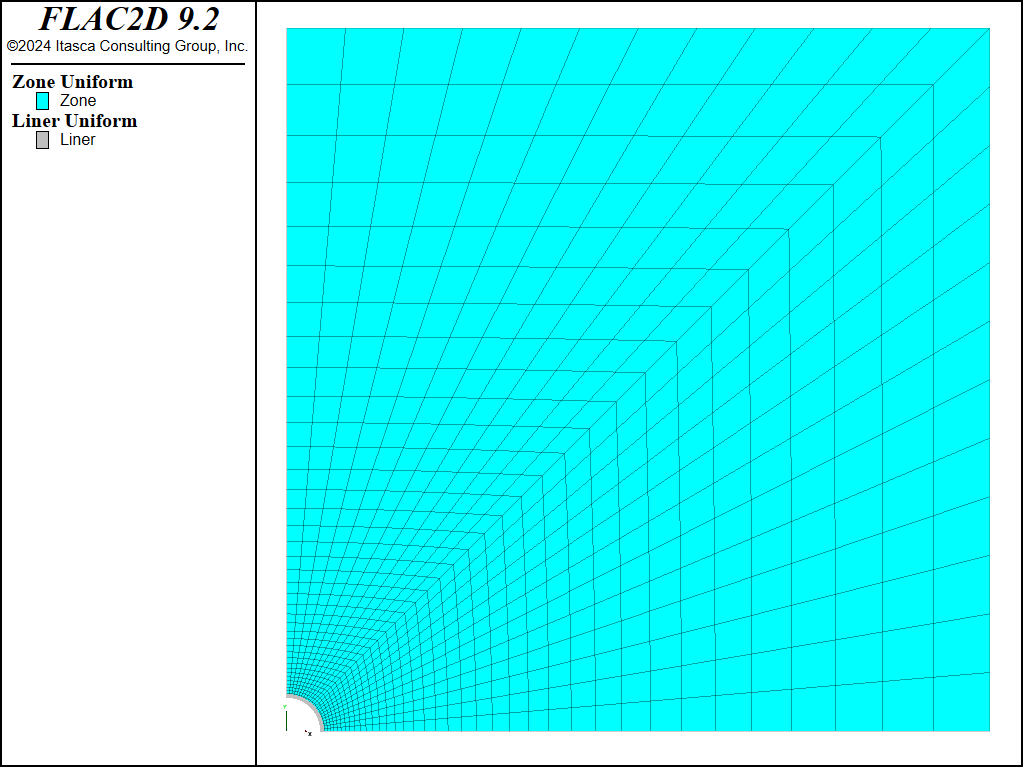
Figure 2: Zones in the FLAC2D model.

Figure 3: Liner elements, nodes, and zones in the FLAC2D model.
Results and Discussion — Qualitative Assessment
We confirm that the coupling deformation is small relative to the zone deformation (and thus confirm that the elastic coupling stiffnesses, \(k_n\) and \(k_s\), are large enough) by plotting the displacements of the gridpoints and nodes at the tunnel crown and springline (see Figure 4). The relative displacement between the gridpoints and nodes is small compared with the gridpoint displacement.
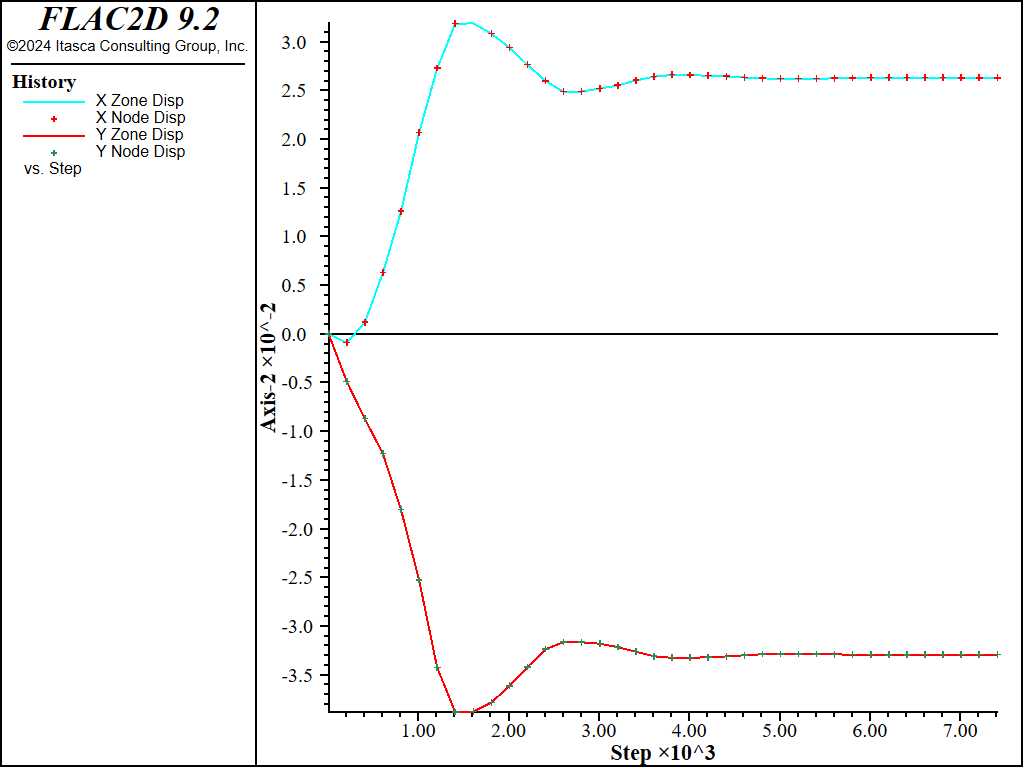
Figure 4: Displacements of gridpoints and nodes at tunnel crown and springline for no-slip case.
If the model is run with no support (by deleting the liner elements), the tunnel crown and springline both move inward (see Figure 5). When the support is included, the tunnel crown still moves inward, but the tunnel springline moves outward (see Figure 6), because the support resists the inward ground movement. If the liner is allowed to slip at the support-ground coupling (by setting the liner property of coupling-cohesion-shear equal to zero), a relative shearing motion occurs between the liner and the ground (see Figure 7).
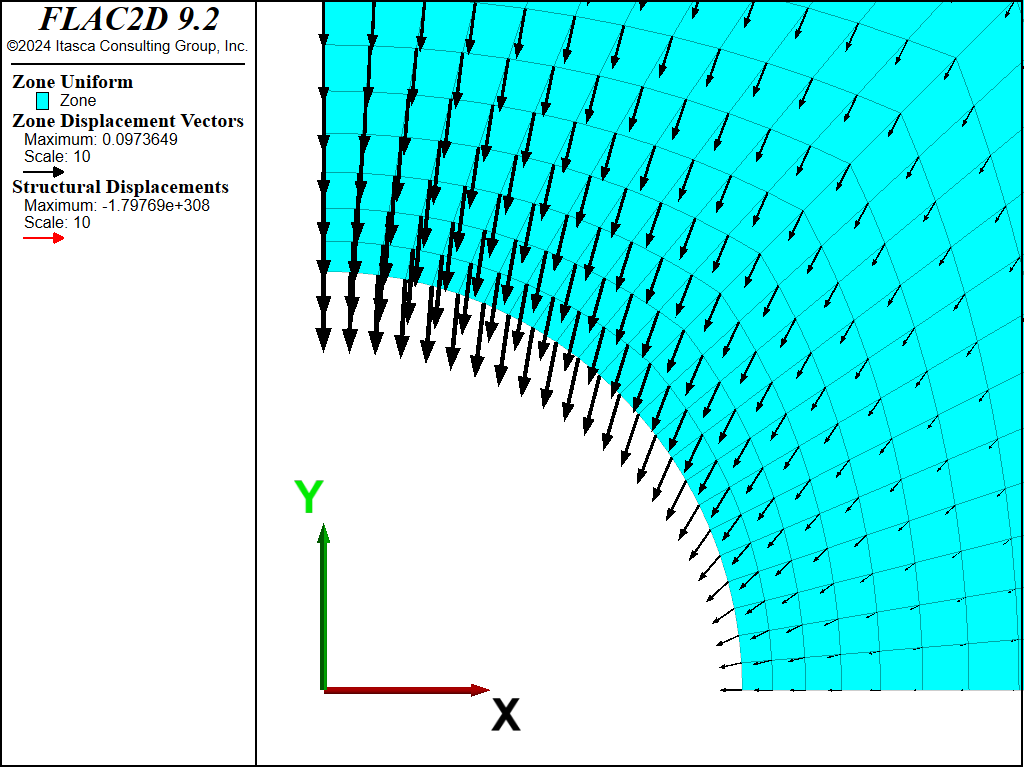
Figure 5: Displacement field of ground with no liner present.
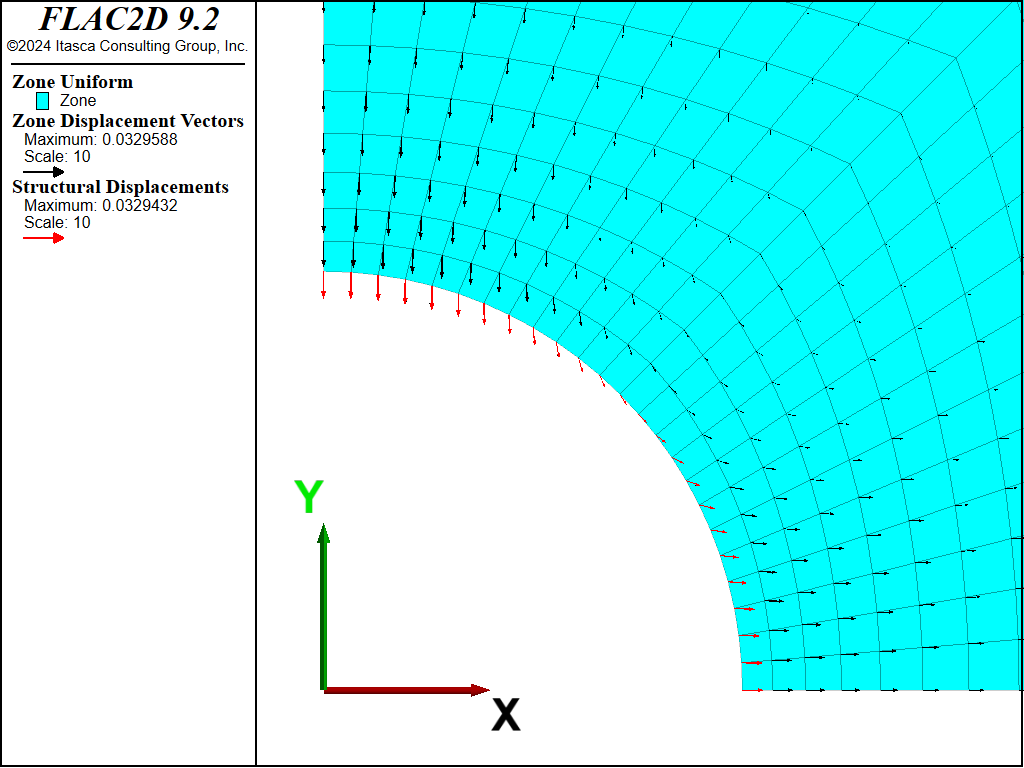
Figure 6: Displacement field of liner and ground (no slip).
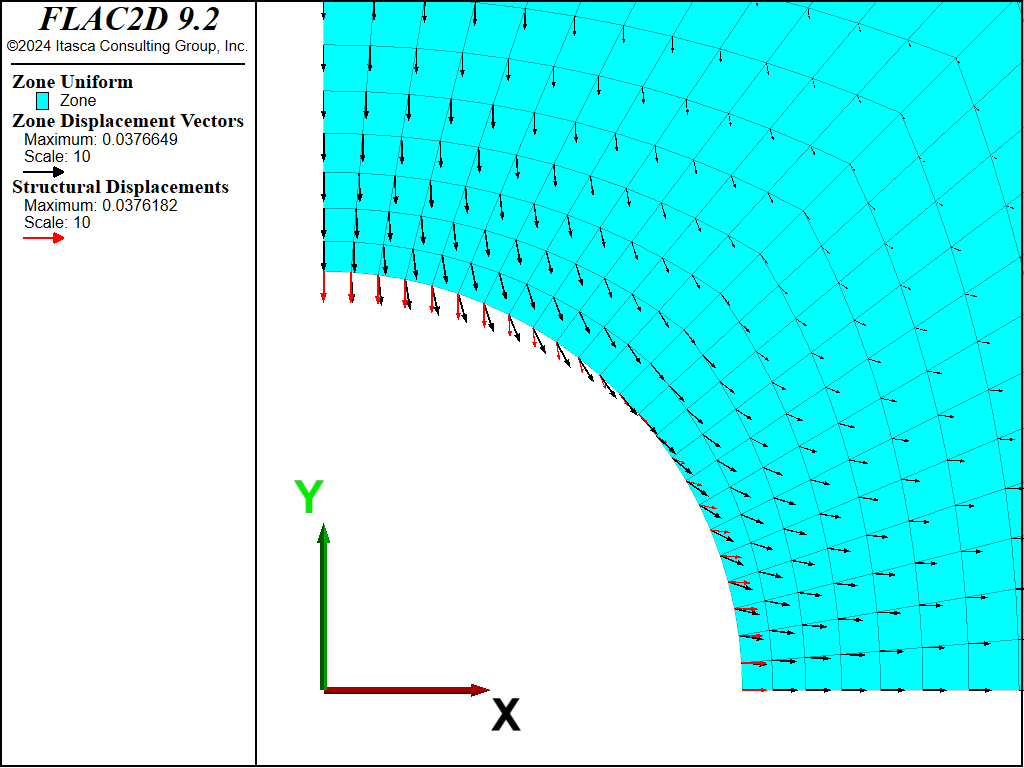
Figure 7: Displacement field of liner and ground (full slip).
The thrust, \(T\), and bending moment, \(M\), in the liner for both the no-slip and full-slip cases are shown in Figures 8 to 11. When the liner is allowed to slip, the thrust becomes more uniform and the bending moment increases slightly. The thrust, \(T\), corresponds to the axial force-x where the \(x\)-direction lies along the tunnel circumference, and the bending moment si given as, \(M\). In these plots, the liner is oriented such that left-to-right corresponds with the angular location \(\theta\) in the closed-form solution varying from zero to ninety degrees. Note that these values of \(T\) and \(M\) are of opposite sign to the values from the analytical solution.
break
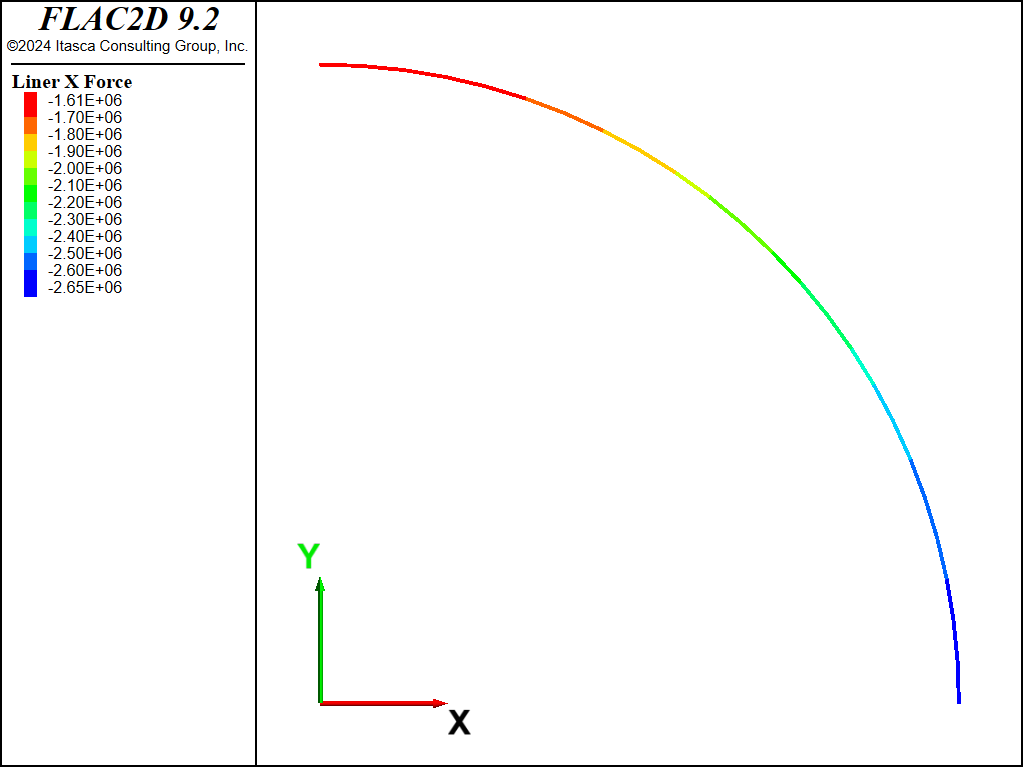
Figure 8: Thrust in liner (no slip).
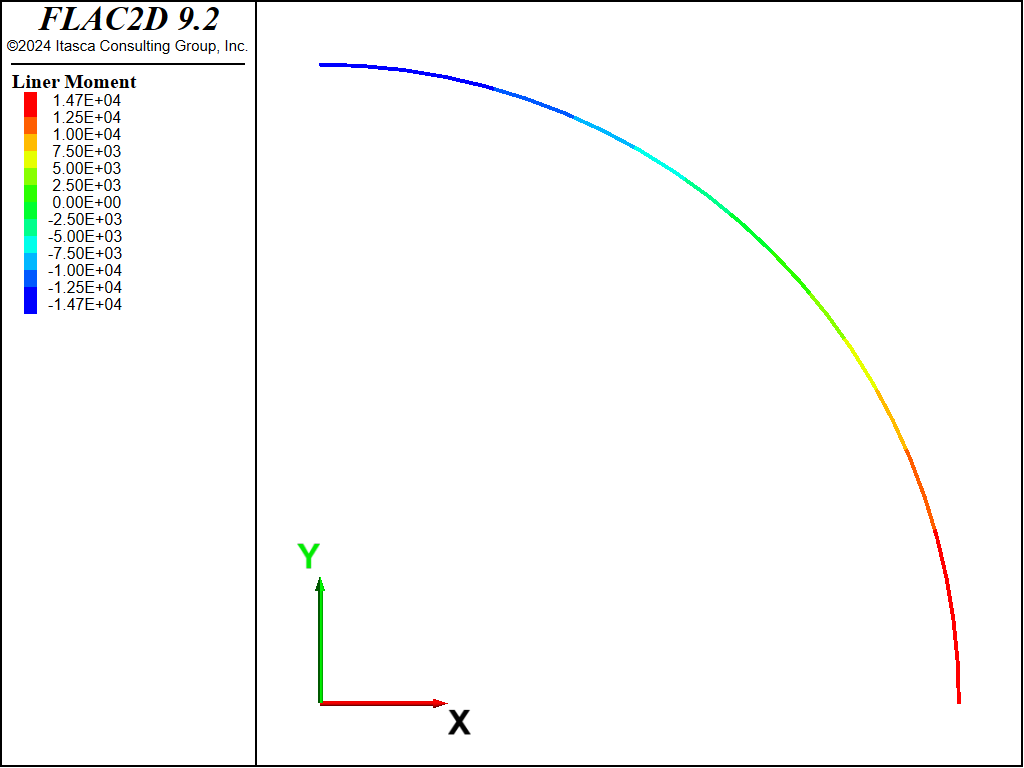
Figure 9: Bending moment in liner (no slip).
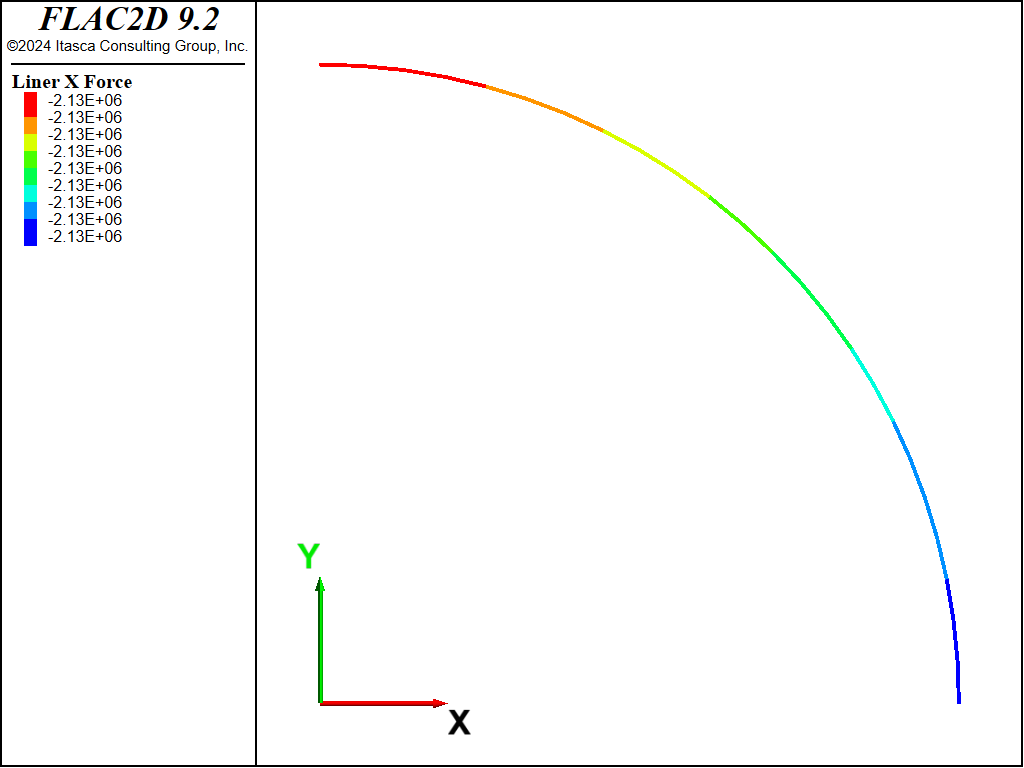
Figure 10: Thrust in liner (full slip).
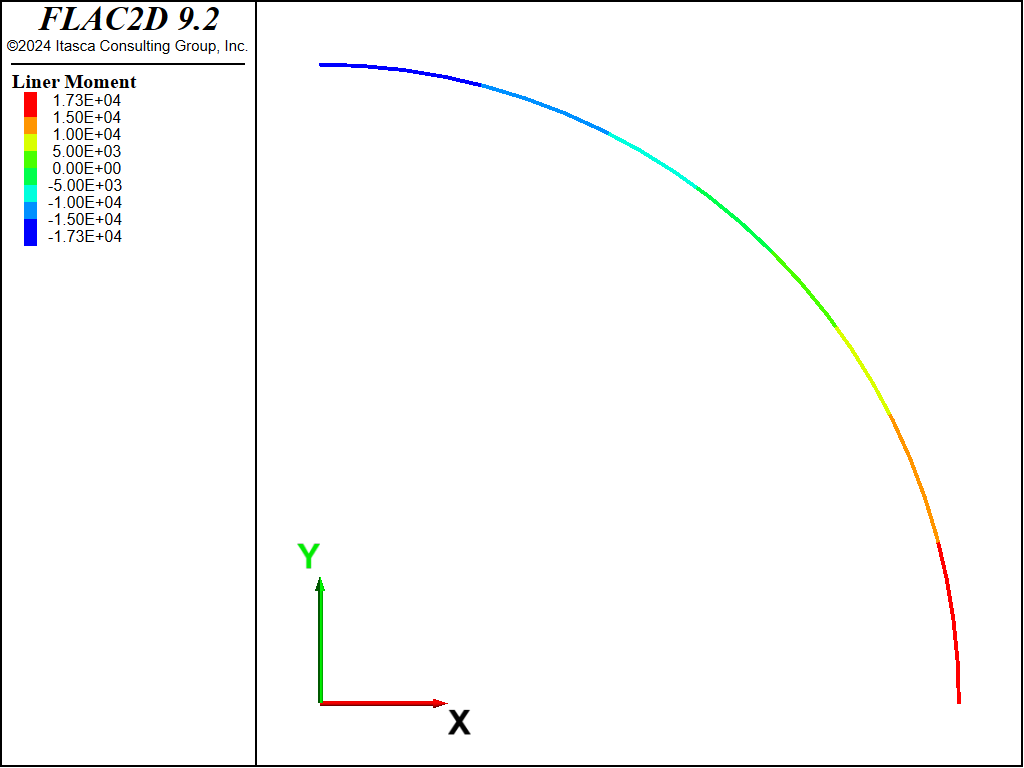
Figure 11: Bending moment in liner (full slip).
The coupling contact stresses, \(\sigma_R\) and \(\tau_{R\theta}\), for both the no-slip and full-slip cases are shown in Figures 12 to 15. These values are obtained from the normal and shear coupling springs that join the liner nodes to the zones. Positive normal stresses indicate separation, and this convention is opposite to that of the analytical solution. The plotted shear stresses depict magnitude only; the direction can be printed or accessed by the FISH functions struct.liner.normal.dir
and struct.liner.shear.dir
.
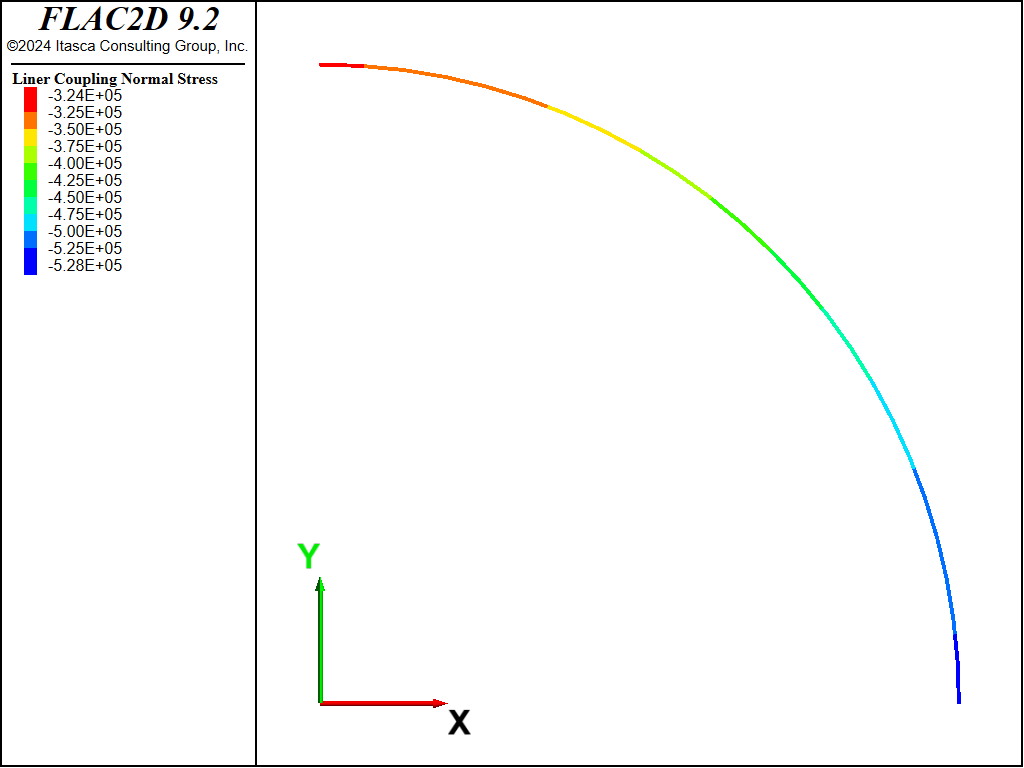
Figure 12: Coupling normal contact stress (no slip).
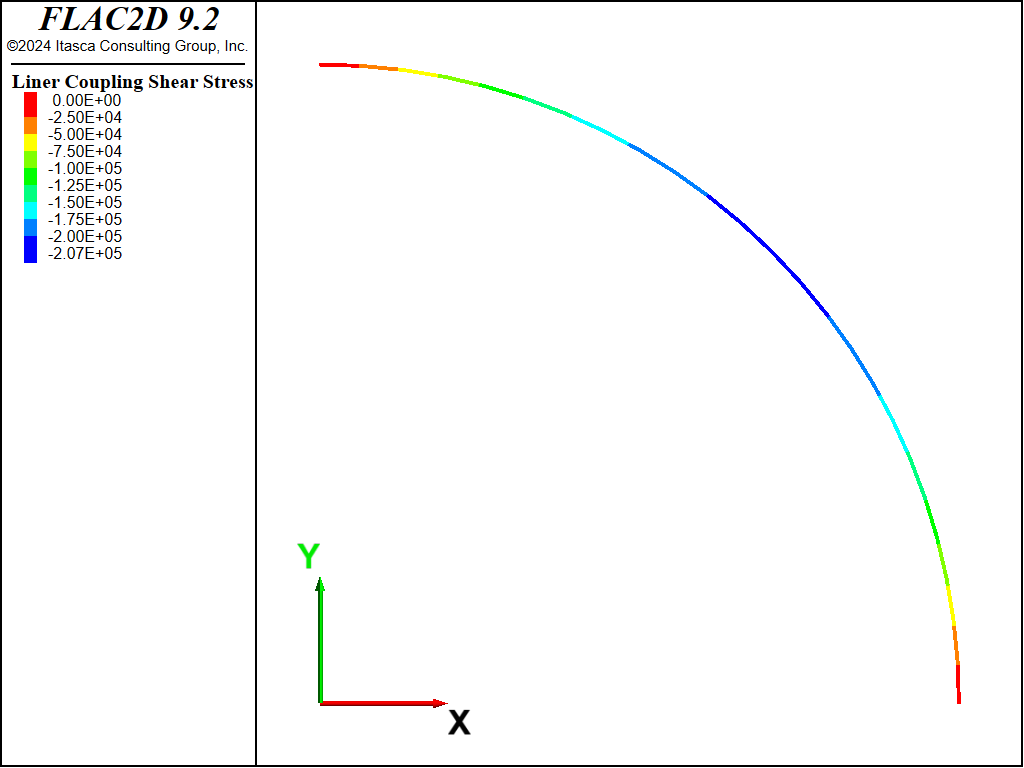
Figure 13: Coupling shear contact stress (no slip).
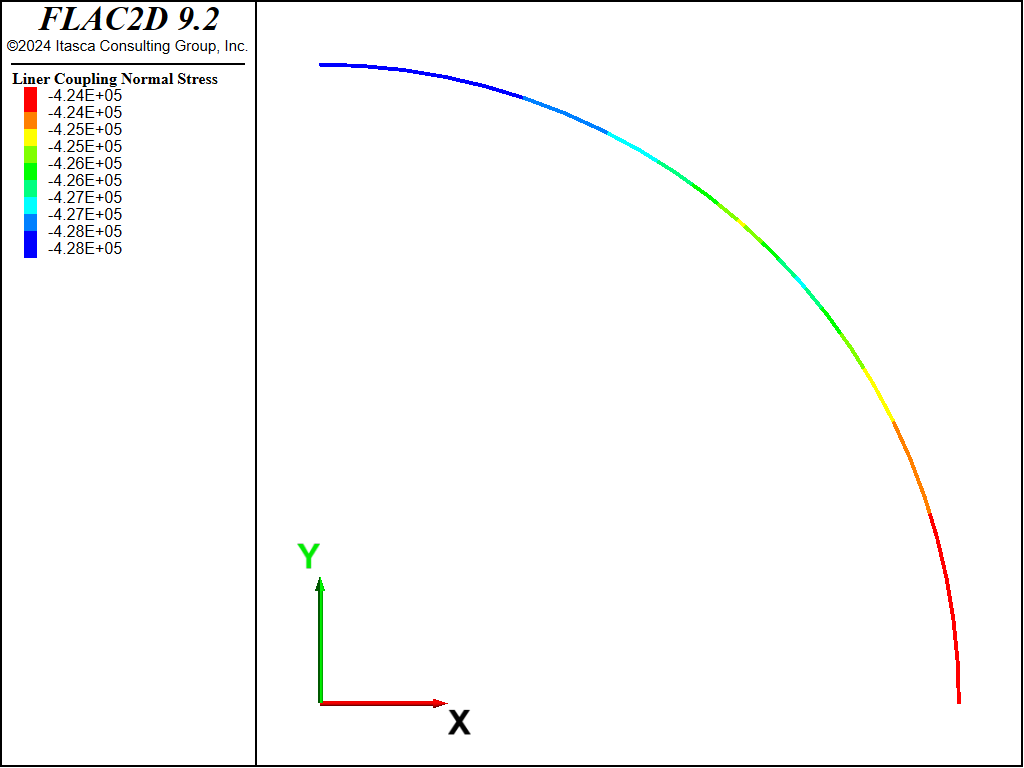
Figure 14: Coupling normal contact stress (full slip).
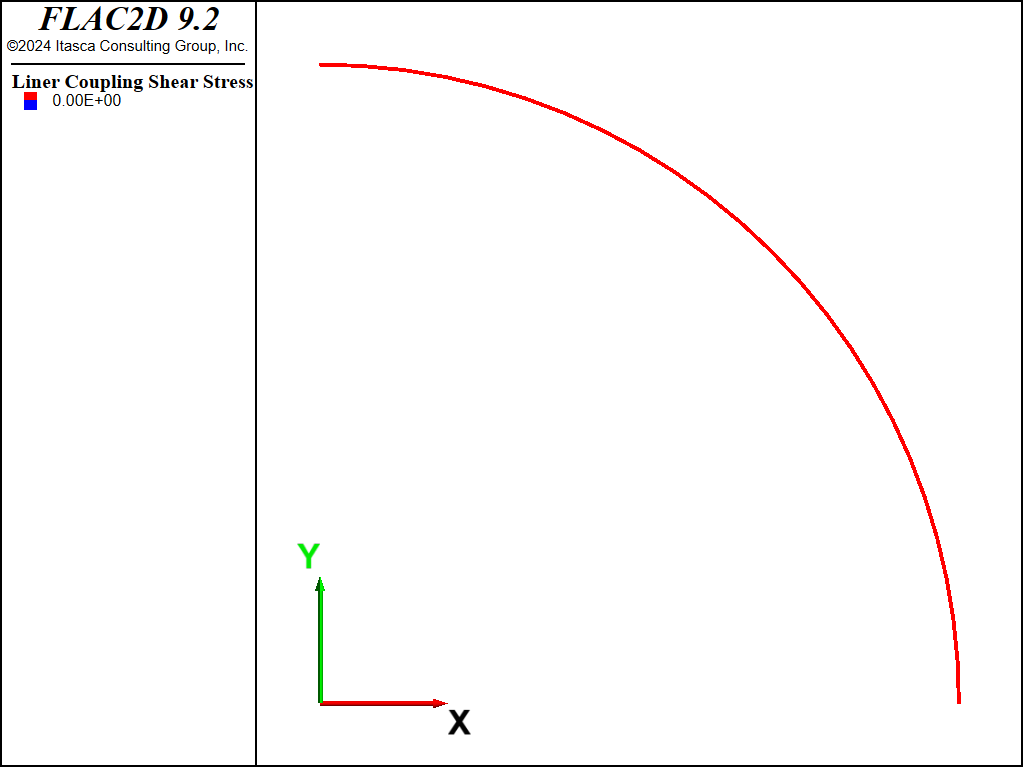
Figure 15: Coupling shear contact stress (full slip).
Results and Discussion — Quantitative Assessment
A quantitative comparison of the support displacements, internal stresses, and coupling contact stresses with the analytical solutions for both the no-slip and full-slip cases is provided in Figures 16 to 24. The FISH functions extract the necessary values from the FLAC2D model and compare them with the analytical values. Either the no-slip or full-slip analytical solution is used by setting the no_slip FISH variable to 1 or 0, respectively. The support displacements (\(u_s\) and \(v_s\)) are sampled at the nodes using the struct.node.disp.global
FISH function. The internal stresses (\(T\) and \(M\)) are sampled at the element midpoints using the struct.beam.force
and struct.beam.moment
functions. Also, the coupling contact stresses (\(\sigma_R\) and \(\tau_{R\theta}\)) are sampled at the element midpoints by computing the average value from the two coupling springs at the element nodes using the struct.liner.normal.stress
and struct.liner.shear.stress
functions.
For both the no-slip and full-slip cases, the responses compare well with the analytical solution. The support displacements match the analytical solution, with a maximum discrepancy of approximately 2% at the tunnel crown. The thrusts match the analytical solution, with a maximum discrepancy of approximately 1.2%. The coupling contact stresses match the analytical solution away from the modeled ends (at \(\theta\) equals 0 and 90 degrees).
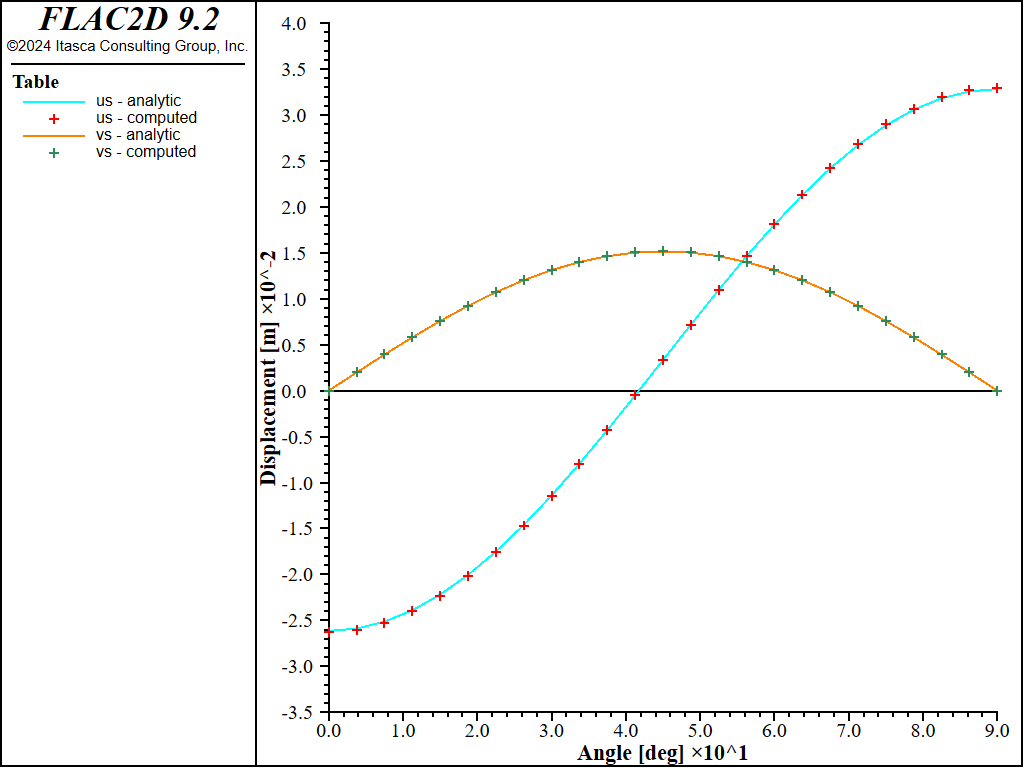
Figure 16: Radial and tangential support displacements versus angle (computed and analytical values, no slip).
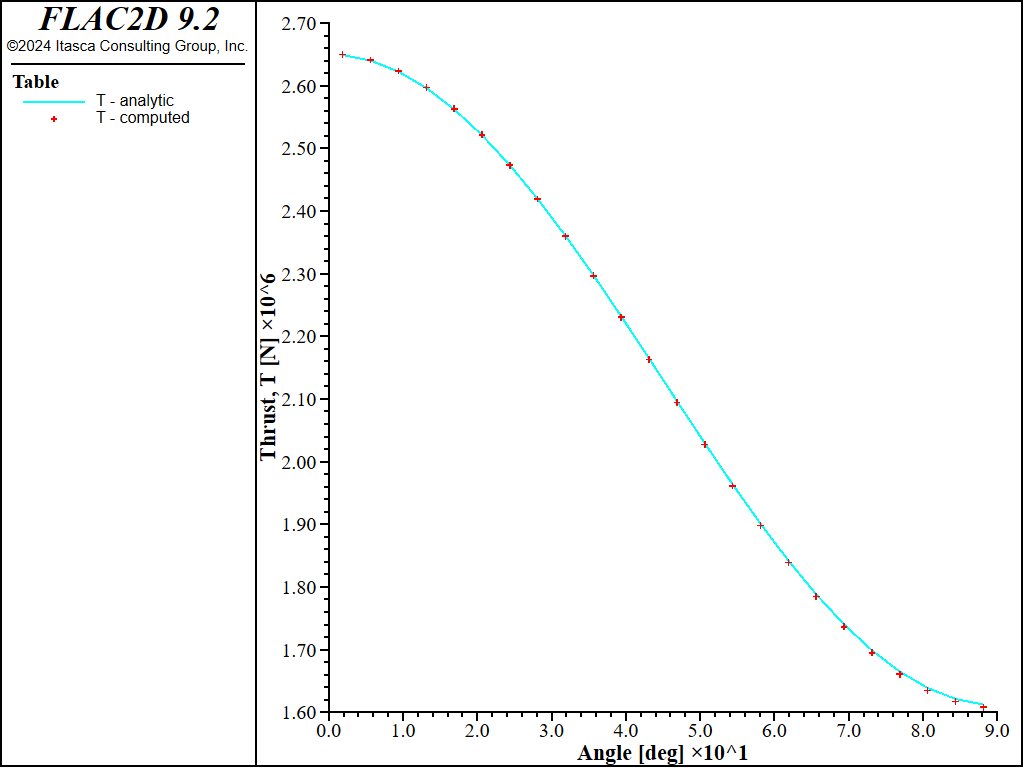
Figure 17: Thrust versus angle (computed and analytical values, no slip).
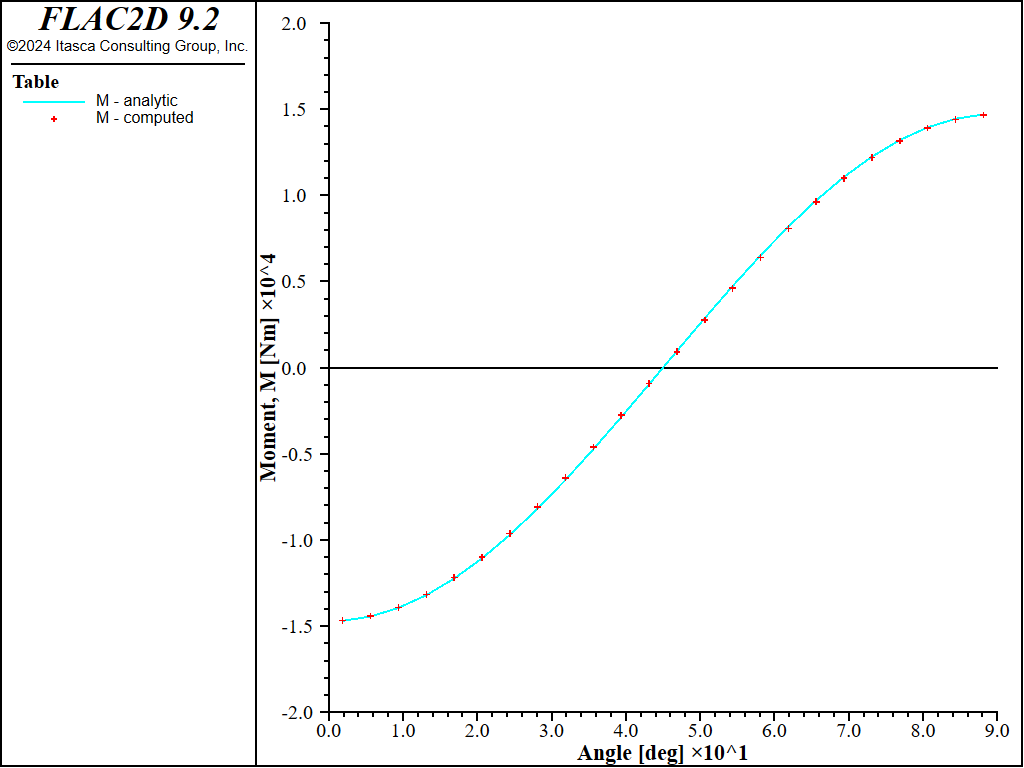
Figure 18: Bending moment versus angle (computed and analytical values, no slip).
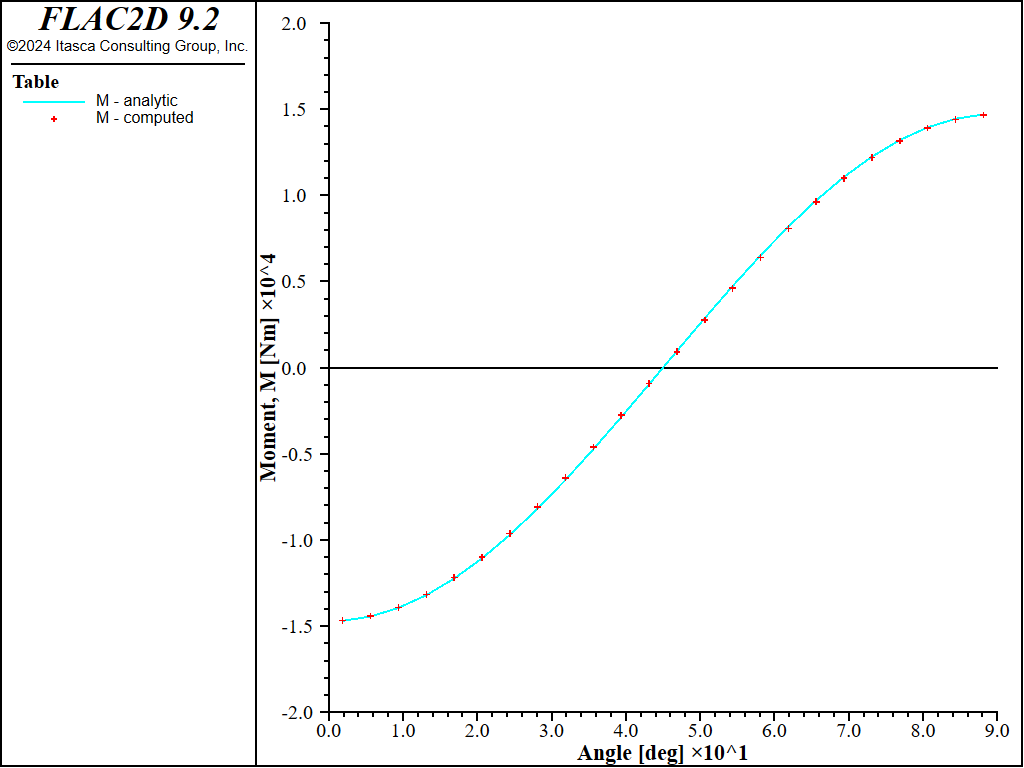
Figure 19: Coupling normal contact stress versus angle (computed and analytical values, no slip).
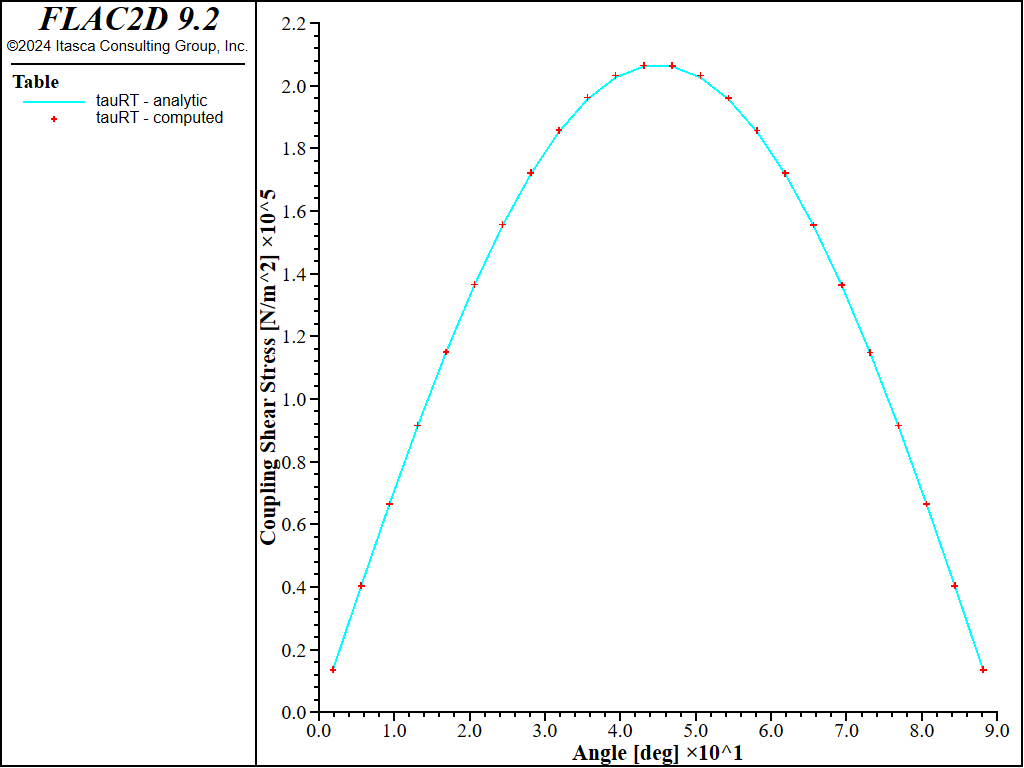
Figure 20: Coupling shear contact stress versus angle (computed and analytical values, no slip).
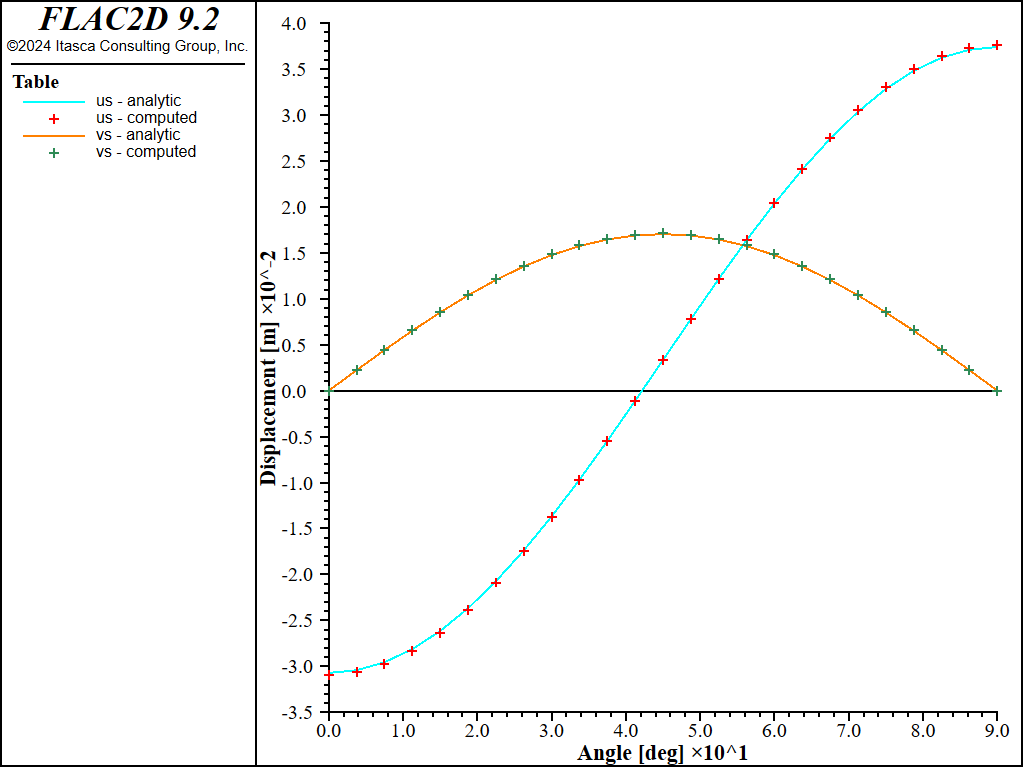
Figure 21: Radial and tangential support displacements versus angle (computed and analytical values, full slip).
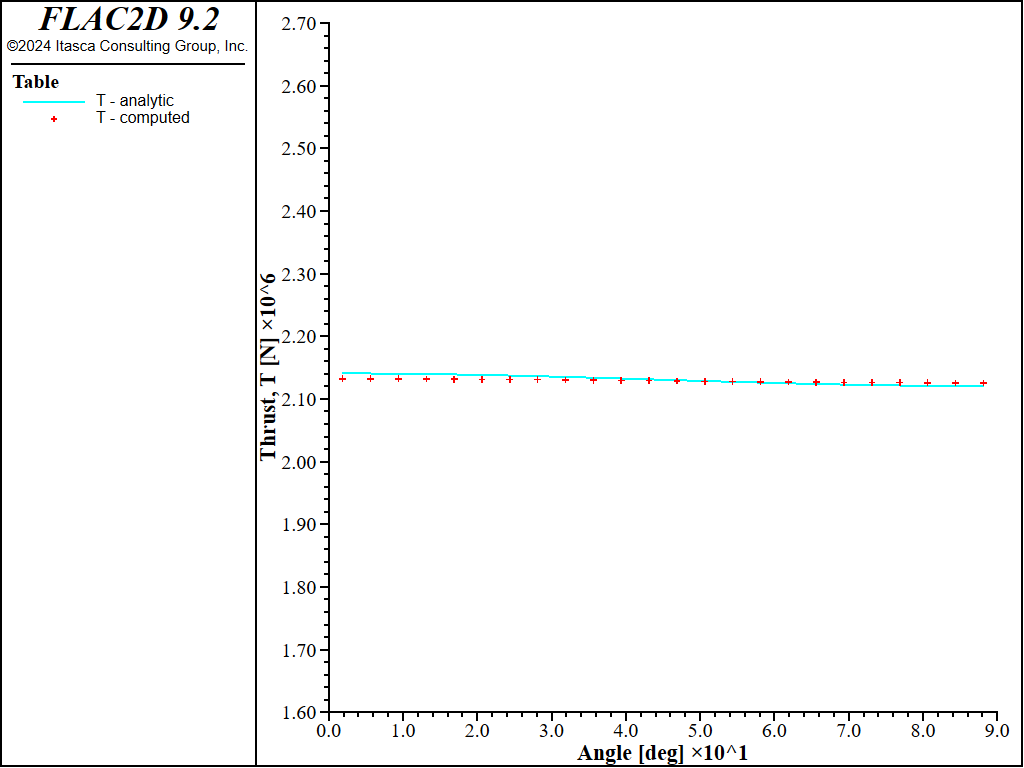
Figure 22: Thrust versus angle (computed and analytical values, full slip).
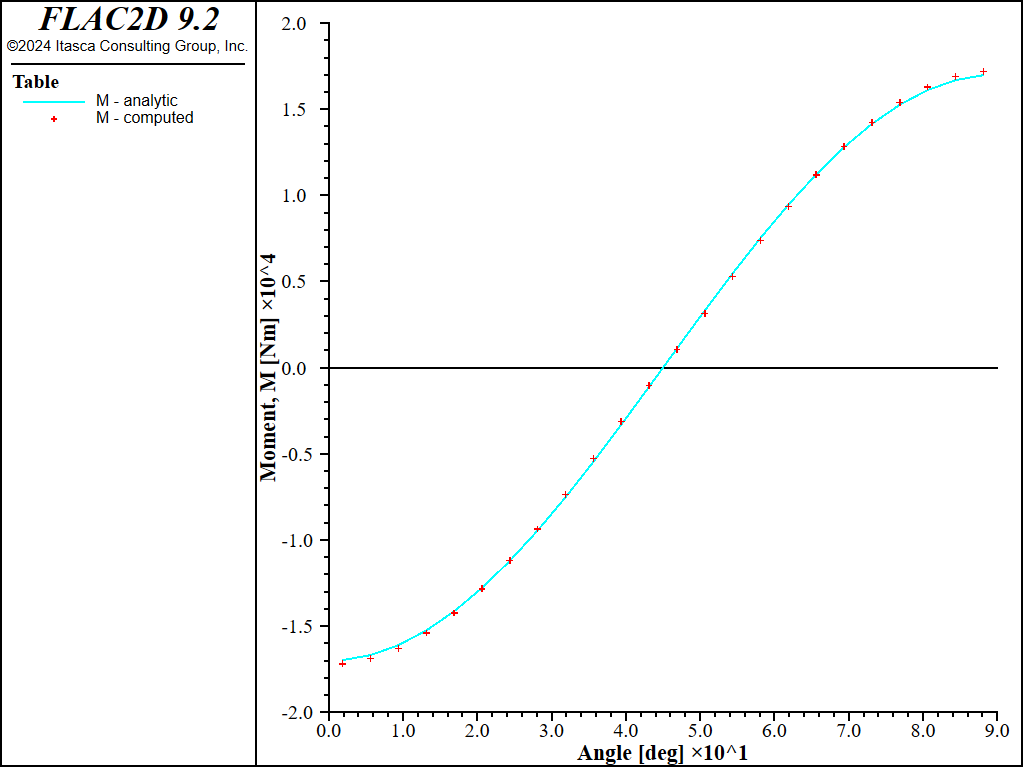
Figure 23: Bending moment versus angle (computed and analytical values, full slip).
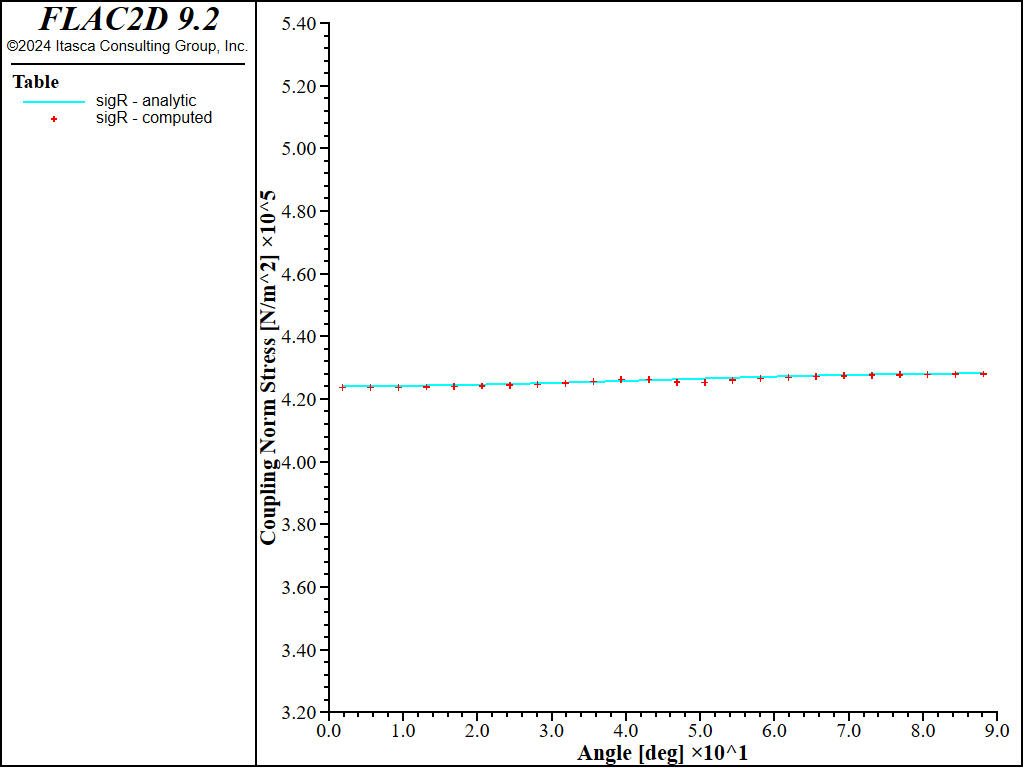
Figure 24: Coupling normal contact stress versus angle (computed and analytical values, full slip).
Reference
Einstein, H. H., and C. W. Schwartz. “Simplified Analysis for Tunnel Supports,” J. Geotech. Engr. Div., 105(GT4): 499-518 (1979).
break
Data File
LinedCircularTunnel.dat
model new
model large-strain off
fish automatic-create off
[global t = 'Lined Circular Tunnel in an Elastic Medium']
[t += ' with Anisotropic Stresses']
model title [t]
; Create the ground mass (zones).
zone create2d sector-quad size 1 24 38 ratio 1 1 1.087 ...
point 1 (100,0) point 2 (0,100) ...
point 3 (100,100) dimension 5 5
; Material model and properties
zone cmodel assign elastic
zone property bulk 5e7 shear 1.791e7
; Name the model boundaries
zone face skin
; Create the support (linerSELs).
structure liner create by-zone-face range group 'West1'
structure liner cmodel assign elastic
structure liner property young 2.5e10 poisson 0.15 ...
cross-sectional-area 0.125 moi [(0.125^3)/12] ...
coupling-stiffness-normal 2.0763e10 ...
coupling-stiffness-shear 2.0763e10 ...
coupling-cohesion-shear 1e20
; Install in-situ stresses in entire grid.
zone initialize stress xx -3e5 zz -3e5 yy -6e5
; Specify boundary conditions.
; Apply stresses at far-field boundaries
zone face apply stress-normal -3e5 range group 'East'
zone face apply stress-normal -6e5 range group 'Top'
; For the grid points (symmetry conditions)
zone face apply velocity-normal 0.0 range group 'West2' or 'Bottom'
; For the nodes (symmetry conditions)
structure node system-local x (-1,0) y (0,-1) range position-x 0; x=0 plane
structure node fix system-local range position-x 0
structure node fix velocity-x rotation range position-x 0
structure node system-local x (0,1) y (-1,0) range position-y 0; y=0 plane
structure node fix system-local range position-y 0
structure node fix velocity-x rotation range position-y 0
;
structure link tolerance-contact 5e-4
; Histories
model history mechanical ratio-local
zone history displacement-x position (5,0); tunnel spring-line
zone history velocity-x position (5,0)
structure node history displacement-x position (5,0)
structure node history velocity-x position (5,0)
zone history displacement-y position (0,5); tunnel crown
zone history velocity-y position (0,5)
structure node history displacement-y position (0,5)
structure node history velocity-y position (0,5)
history interval 10
;
model save 'starting'
; No support case
structure liner delete
model solve convergence 0.1
model title [t]
model save 'No Support'
; Slip case
model restore 'starting'
structure liner property coupling-cohesion-shear 0
model solve convergence 0.1
model title [t + " - Full Slip"]
model save 'Full Slip'
; No slip case
model restore 'starting'
model solve convergence 0.1
model title [t + " - No Slip"]
model save 'No Slip'
Was this helpful? ... | Itasca Software © 2024, Itasca | Updated: Dec 05, 2024 |