Choice of Constitutive Model
All zones in a model must be assigned a constitutive model. In turn, the properties of the model(s) that have been assigned must be set. These two steps make up the work involved in characterizing the material that makes up the model, and there are a number of considerations to be taken into account. This section examines the constitutive model selection and assignment process. The next, Material Properties, covers the subject of property assignment.
All of the examples listed in this section are included in the project file “ConstitutiveModels.prj.”
Overview of Constitutive Models
This section provides an overview of the constitutive models in FLAC3D and makes recommendations concerning their appropriate application. The Constitutive Models section presents background information on the model formulations.
The built-in mechanical material models [1] in FLAC3D are:
- Null;
- (Isotropic) elasticity;
- Orthotropic elasticity;
- Anisotropic (transversely isotropic) elasticity;
- Drucker-Prager plasticity;
- Mohr-Coulomb plasticity;
- Ubiquitous-joint plasticity;
- Anisotropic-elasticity ubiquitous-joint plasticity;
- Strain-hardening/softening Mohr-Coulomb plasticity;
- Bilinear strain-hardening/softening ubiquitous-joint (SUBI) plasticity;
- Double-yield plasticity;
- Modified Cam-clay plasticity;
- Hoek-Brown plasticity;
- Hoek-Brown-PAC plasticity;
- Cap-Yield (CYSoil) plasticity;
- Simplified Cap-Yield (CHSoil) plasticity;
- Plastic-Hardening (PH) plasticity;
- Swell plasticity; and
- Mohr-Coulomb Tension Crack plasticity.
Each model is developed to represent a specific type of constitutive behavior commonly associated with geologic materials. The null model is used to represent material that is removed from the model. The isotropic elasticity model is valid for homogeneous, isotropic, continuous materials that exhibit linear stress-strain behavior. The orthotropic elasticity model and the anisotropic (transversely isotropic) elasticity model are appropriate for elastic materials that exhibit well-defined elastic anisotropy. The Drucker-Prager plasticity model is a simple failure criterion in which the shear yield stress is a function of isotropic stress. The Mohr-Coulomb plasticity model is used for materials that yield when subjected to shear loading, but the yield stress depends on the major and minor principal stresses only; the intermediate principal stress has no effect on yield. The ubiquitous-joint plasticity model corresponds to a Mohr-Coulomb material that exhibits a well-defined strength anisotropy due to embedded planes of weakness. The Anisotropic-elasticity ubiquitous-joint plasticity model is extended from the ubiquitous-joint plasticity model by taking the anisotropic elasticity into account. The strain-hardening/softening Mohr-Coulomb plasticity model is based upon the Mohr-Coulomb model, but is appropriate for materials that show an increase or degradation in shear strength when loaded beyond the initial failure limit. The SUBI plasticity model is a generalization of the ubiquitous-joint model that allows the strength properties for the matrix and the joint to harden or soften. The double-yield plasticity model is an extension of the strain-softening model to simulate irreversible compaction as well as shear yielding. The modified Cam-clay plasticity model accounts for the influence of volume change on deformability and on resistance to failure. The Hoek-Brown plasticity model is an empirical relation that is a nonlinear failure surface representing the strength limit for isotropic intact rock and rock masses. Its non-linear failure surface is continuously approximated by the Mohr-Coulomb tangent at the current minimum principle stress level. It can be used to perform factor of safety calculations. The Hoek-Brown-PAC plasticity model is based on the traditional Hoek-Brown nonlinear failure surface but also includes a plasticity flow rule that varies as a function of the confining stress level. The CYSoil plasticity model provides a comprehensive representation of the nonlinear behavior of soils considering both frictional and volumetric hardening. The CHSoil plasticity model is a simplified version of the CYSoil plasticity model by neglecting the volumetric hardening. The Plastic-Hardening plasticity model is a shear and volumetric hardening constitutive model for the simulation of soil behavior using a curved pre-failure stress-strain relation. The model is straightforward to calibrate using either conventional lab tests or in-situ tests. It is well established for soil-structure interaction problems, excavations, tunneling, and settlements analysis, among many other applications. The Swell plasticity model is based on the Mohr-Coulomb model with nonassociated shear and associated tension flow rules. The difference is that the wetting-induced deformations are taken into account by means of coupling wetting strains with the model state prior to wetting. The Mohr-Coulomb Tension Crack plasticity model is an extension of the Mohr-Coulomb constitutive model that considers tensile plastic strains to be reversible and prevents generation of compressive normal stresses (perpendicular to cracks) before cracks close.
The material models in FLAC3D are primarily intended for applications related to geotechnical engineering (e.g., underground construction, mining, slope stability, foundations, earth and rock-fill dams). When selecting a constitutive model for a particular engineering analysis, the following two considerations should be kept in mind:
- What are the known characteristics of the material being modeled?
- What is the intended application of the model analysis?
The table below presents a summary of the FLAC3D models along with examples of representative materials and possible applications of the models. The Mohr-Coulomb model is the most applicable for general engineering studies. Also, Mohr-Coulomb parameters for cohesion and friction angle are usually available more often than other properties for geo-engineering materials. The ubiquitous-joint, strain-softening, bilinear strain-softening/ubiquitous-joint, and double-yield plasticity models are actually variations of the Mohr-Coulomb model. These models will produce results identical to those for Mohr-Coulomb if the additional material parameters are set to high values. The Drucker-Prager model is a simpler failure criterion than Mohr-Coulomb, but it is not generally suitable for representing failure of geologic materials. It is provided mainly to allow comparison of FLAC3D to other numerical programs that have the Drucker-Prager model but not the Mohr-Coulomb model. Note that, at zero friction, the Mohr-Coulomb model degenerates to the Tresca model, while the Drucker-Prager model degenerates to the von Mises model.
The Drucker-Prager and Mohr-Coulomb models are the most computationally efficient plasticity models; the other plasticity models require increased memory and additional time for calculation. For example, plastic strain is not calculated directly in the Mohr-Coulomb model. If plastic strain is required, the strain-softening, bilinear ubiquitous-joint or double-yield model must be used. These three models are primarily intended for applications in which the post-failure response is important (e.g., yielding pillars, caving, or backfilling studies).
The Constitutive Models in FLAC3D
Model | Representative Material | Example Application |
---|---|---|
null | void | holes, excavations, regions in which material will be added at later stage |
elastic | homogeneous, isotropic continuum; linear stress-strain behavior | manufactured materials (e.g., steel) loaded below strength limit; factor of safety calculation |
orthotropic elastic | materials with three mutually perpendicular planes of elastic symmetry | columnar basalt loaded below strength limit |
transversely isotropic elastic | thinly laminated material exhibiting elastic anisotropy (e.g., slate) | laminated materials loaded below strength limit |
Drucker-Prager | limited application; soft clays with low friction | common model for comparison to implicit finite-element programs |
Mohr-Coulomb | loose and cemented granular materials; soils, rock, concrete | general soil or rock mechanics (e.g., slope stability and underground excavation) |
strain-hardening/softening Mohr-Coulomb | granular materials that exhibit nonlinear material hardening or softening | studies in post-failure (e.g., progressive collapse, yielding pillar, caving) |
ubiquitous-joint | thinly laminated material exhibiting strength anisotropy (e.g., slate) | excavation in closely bedded strata |
anisotropic-elasticity ubiquitous-joint | thinly laminated material exhibiting stiffness and strength anisotropy (e.g., slate) | excavation in closely bedded strata |
bilinear strain-hardening/softening ubiquitous-joint | laminated materials that exhibit nonlinear material hardening or softening | studies in post-failure of laminated materials |
double-yield | lightly cemented granular material in which pressure causes permanent volume decrease | hydraulically placed backfill |
modified Cam-clay | clay | geotechnical construction on clay |
Hoek-Brown | isotropic rock material | geotechnical construction in rock; factor-of-safety calculation |
Hoek-Brown-PAC | isotropic rock material | geotechnical construction in rock |
CYSoil and CHSoil | soils | excavation, tunnel, slope stability, embankment, foundation analysis |
Plastic-Hardening | soils | excavation, tunnel, slope stability, embankment, foundation analysis |
swell | soils with wetting-induced deformations | application on soils where wetting-induced deformations are significant |
Mohr-Coulomb-Tension | rocks and soils | dynamic response or deformation of the overburden above the undercut |
The tensile failure criterion is identical in the Drucker-Prager, Mohr-Coulomb, ubiquitous-joint, anisotropic-elasticity ubiquitous-joint, strain-softening, bilinear strain-softening/ubiquitous-joint, double-yield, and swell models. This criterion defines a tensile strength separately from the shear strength, and an associated flow rule for the onset of tensile failure. For the Drucker-Prager, Mohr-Coulomb, and ubiquitous-joint models, the value assigned to the tensile strength remains constant by default when tensile failure occurs, although the flag-brittle property can be used to reduce the tension limit to 0 after tensile failure. Tensile softening can be modeled with the strain-softening, bilinear strain-softening ubiquitous-joint and double-yield models. (see the Post-Failure Properties topic.) Note that no record is made of notional voids that may open after tensile failure and tensile strain; if the strain rate becomes compressive, all models start to take compressive load immediately—except for the Mohr-Coulomb-Tension model, which was explicitly formulated to overcome this.
The double-yield and modified Cam-clay models both take into account the influence of volumetric change on material deformability and failure characteristics. In both models, tangential bulk and shear moduli are functions of plastic volumetric deformation. The double-yield model was initially developed to represent the behavior of mine backfill material, for which pre-consolidation pressures are low. The modified Cam-clay model is more applicable to soils such as soft clays for which pre-consolidation pressures can have a significant effect on material behavior. The comparison between the double-yield model and modified Cam-clay model is summarized here.
The Hoek-Brown model approximates the non-linear failure surface by the Mohr-Coulomb tangent at the current minor compression principle stress level so that it keeps all merits of the traditional Mohr-Coulomb model, e.g., for factor-of-safety calculations. The Hoek-Brown-PAC model combines the generalized Hoek-Brown criterion with a plasticity flow rule that varies as a function of the confining stress level. At low confining stress, the volumetric expansion at yield is high, associated with axial splitting and wedging effects. At high confining stress, the material approaches a non-dilatant condition.
The CYSoil and PH models both consider friction and volumetric hardening, curved pre-failure behavior, and different unloading stiffness from the loading stiffness, so they are useful in the geotechnical application where the pre-failure and/or excavation-induced deformations are important, e.g., braced/anchored excavation wall design and tunnel construction. The comparison between the PH model and CYSoil model is summarized here.
Selection of an Appropriate Model
A problem analysis should always start with the simplest material model; in most cases, an elastic model should be used first. This model runs the fastest and only requires two material parameters: bulk modulus and shear modulus (see Material Properties). The model provides a simple perspective of stress-deformation behavior in the FLAC3D grid, and can define locations where stress concentrations may develop. This may help to define zoning density for the grid.
It is often helpful to run a simple test of the selected material model before using it to solve the full-scale, boundary-value problem. This can provide insight into the expected response of the model compared to the known response of the physical material.
The following example illustrates the use of a simple test model. The problem application is the analysis of yielding mine pillars. A simple model is created to evaluate the implementation of the Mohr-Coulomb model versus the strain-softening model. This test also illustrates the effect of the selected measurement location on the reported results. The model is a compression test performed on a cylindrical grid composed of Mohr-Coulomb material.
Compression test on Mohr-Coulomb material
model new
model large-strain off
; Create zones
zone create cylinder point 0 (0,0,0) point 1 (1,0,0) ...
point 2 (0,2,0) point 3 (0,0,1) size 4 5 4
zone reflect normal (1,0,0)
zone reflect normal (0,0,1)
; Constitutive Model and properties
zone cmodel assign mohr-coulomb
zone property bulk 1.19e10 shear 1.1e10
zone property cohesion 2.72e5 friction 44 tension 2e5
; Boundary Conditions
zone face apply velocity (0, 1e-7,0) range position-y 0
zone face apply velocity (0,-1e-7,0) range position-y 2
; Histories
zone history displacement-y position (0,0,0)
zone history stress-yy position (0,1,0)
zone history stress-yy position (1,1,0)
model step 3000
model save 'Compression'
The axial (\(y\)-direction) stress-displacement response is monitored at the center and outer boundary in the grid. The results are shown in the figure below.
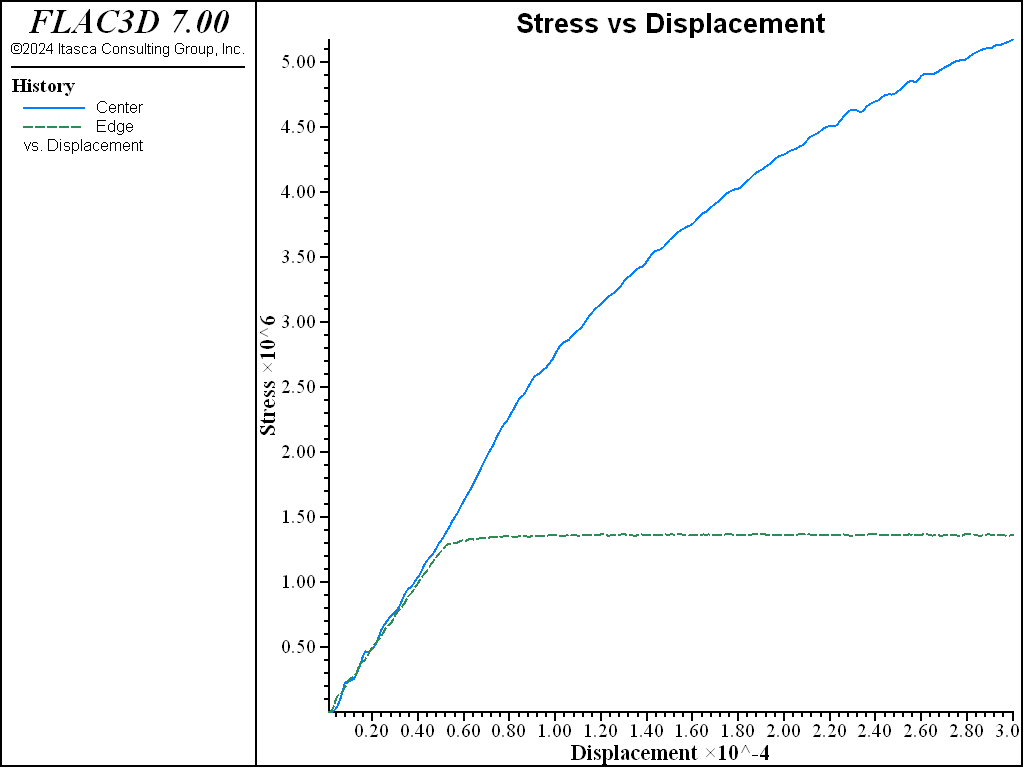
Figure 1: Stress-displacement plots for compression of Mohr-Coulomb material. Response is shown for an interior location (upper curve) and a boundary location (lower curve).
The test is now repeated with the strain-softening model.
Compression test on strain-softening material
model new
model large-strain off
; Create zones
zone create cylinder point 0 (0,0,0) point 1 (1,0,0) ...
point 2 (0,2,0) point 3 (0,0,1) size 4 5 4
zone reflect normal (1,0,0)
zone reflect normal (0,0,1)
; Constitutive Model and properties
zone cmodel assign strain-softening
zone property bulk 1.19e10 shear 1.1e10
zone property cohesion 2.72e5 friction 44 tension 2e5
zone property table-cohesion 'coh' table-friction 'fri'
table 'coh' add (0,2.72e5) (1e-4,2e5) (2e-4,1.5e5) (3e-4,1.03e5) (1,1.03e5)
table 'fri' add (0,44) (1e-4,42) (2e-4,40) (3e-4,38) (1,38)
; Boundary Conditions
zone face apply velocity (0, 1e-7,0) range position-y 0
zone face apply velocity (0,-1e-7,0) range position-y 2
; Histories
zone history displacement-y position (0,0,0)
zone history stress-yy position (0,1,0)
zone history stress-yy position (1,1,0)
model step 3000
model save 'Softening'
The horizontal stress-displacement response is monitored again, as shown in the image below. This test produces distinct peak and residual failure stress levels.

Figure 2: Stress-displacement for compression test of strain-softening material (similar monitoring points to those in the previous image).
The strain-softening model assumes both a brittle softening (due to reduction in cohesion) and a gradual softening (due to a reduction in friction angle). The selection of the properties is discussed further in Material Properties.
Comparison of the two images above illustrates the different responses of the two models. The initial response up to the onset of failure is identical, but post-failure behavior is quite different. Clearly, more data are required to use the strain-softening model and, typically, the softening model must be calibrated for each specific problem.
The effect of confinement on the “measured” response is also demonstrated from these plots. The history recorded in the middle of the grid shows that a higher stress level develops in the center of the model than at the free side. The location of monitoring points should correspond as closely as possible to the location of measurements in the physical problem.
The Effect of Water
Geologic materials generally appear weaker when the pore spaces contain a pore fluid under pressure. This is represented in FLAC3D by the incorporation of an effective stress that accounts for the presence of pore pressure in a zone. The pore pressures in FLAC3D are taken to be positive in compression. Thus, the effective stress \(\sigma^{\prime}\) is related to the total stress \(σ\) and pore pressure \(p\) by
Effective stresses are used in all of the plasticity models.
The effect of water can be seen by repeating the strain-softening example in the preceding topic, but with constant pore pressure in the zones (i.e., an undrained compression test). Add the command
zone face apply velocity (0,-1e-7,0) range position-y 2
; Initial Conditions
to the example before stepping. The lower strength is seen below.
Ways to Implement Constitutive Models
There are several different ways a constitutive model can be implemented in FLAC3D. The standard way is to invoke one of the built-in models with the zone cmodel assign
command. The user-defined models described in Writing New Constitutive Models are also invoked with the zone cmodel assign
command.
The source codes for the built-in models are included in the “\pluginfiles\cmodels” sub-directory, and are also copied to the application data location provided by the user the first time the program is launched. These files should be reviewed as examples for users who wish to write and implement their own models. User-defined models are written in C++ and are implemented as DLLs that are loaded with the FLAC3D executable file in the same manner as the built-in models.[2] (See Writing New Constitutive Models.)
Often, it is desirable to modify an existing constitutive model (either a built-in model or a user-defined model) to make material properties dependent on other model parameters. There are three ways this can be done:
- change properties of the built-in model via a FISH function that scans all the zones and is called at a specified step increment (say, every ten steps);[3]
- change properties in a user-defined constitutive model function at every step by reference to a formula; or
- change properties via look-up tables (with table commands) that modify strength properties as a function of plastic strain for the built-in strain-softening and double-yield models.
The third approach is the most efficient way to change properties in a FLAC3D model. The first approach is the least efficient.
Endnotes
[1] | Users can create their own constitutive models as DLLs by following the procedures given in Writing New Constitutive Models. Also available are nine optional models that simulate viscoelastic and viscoplastic, time-dependent (creep) behavior (see Description of Creep Constitutive Models), and two optional models to simulate dynamic pore-pressure generation (see Dynamic Analysis). |
[2] | Note that this approach differs from the FISH constitutive model used in two-dimensional FLAC. With the DLL approach, user-defined models run at the same calculational speed as built-in models. |
[3] | Note that increasing stiffness properties requires that a general update be performed in order to preserve stability. The zone.force.update function will force a general update to be performed at the start of the next cycle. |
Was this helpful? ... | FLAC3D © 2019, Itasca | Updated: Feb 25, 2024 |