Liner Structural Elements
Note that shell structural elements are based on the Shell-Type Structural Element and share the underlying formulation and implementation.
Mechanical Behavior
Single-Side Liner-Grid Interaction
The mechanical behavior of each liner element can be divided into the structural response of the liner material itself (see Shell-Type Mechanical Behavior), and the way in which the liner element interacts with the FLAC3D grid. By default, liner elements are assigned the DKT-CST shell element that resists both membrane and bending loading (see Shell Finite Elements). A physical liner can be modeled as a collection of liner elements that are attached to the surface of the FLAC3D grid. In addition to providing the structural behavior of a shell, a shear-directed (in the tangent plane to the liner surface) frictional interaction occurs between the liner and the FLAC3D grid. Also, in the normal direction, both compressive and tensile forces can be carried, and the liner may break free from (and subsequently come back into contact with) the grid. Liners are used to model thin liners for which both normal-directed compressive/tensile interaction and shear-directed frictional interaction with the host medium occurs, such as shotcrete-lined tunnels or retaining walls.
The orientation of the node-local system for all nodes used by liner elements is set automatically at the start of a set of cycles (or when the model cycle
0 command is executed) such that the \(z\)-axis is aligned with the average normal direction of all liner elements using the node, and the \(xy\)-axes are arbitrarily oriented in the liner element tangent plane (see Figure 2 (a)).
A liner is attached to the surface of the FLAC3D grid. The behavior at the liner-zone interface is summarized in Figure 1 to 2. The stresses acting on the liner are shown in Figure 1. These stresses, consisting of a normal stress, \(\sigma_n\), and a shear stress, \(\tau\), are balanced by stresses that develop within the liner itself (these stress resultants — see Stresses in Shells — are denoted by \(\bar R\) in Figure 2). The interface behavior is represented numerically at each liner node by a linear spring with finite tensile strength in the normal direction, and a spring-slider in the tangent plane to the liner surface. The orientation of the spring-slider changes in response to relative shear displacement \({\bf u}_s\) between the liner and the host medium, as shown in Figure 2. (Note that the liner is drawn below the zones in Figure 1 and above the zones in Figure 2.)
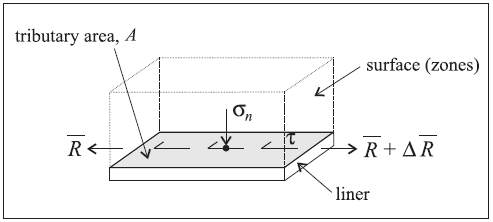
Figure 1: Stresses acting on the liner elements surrounding a node
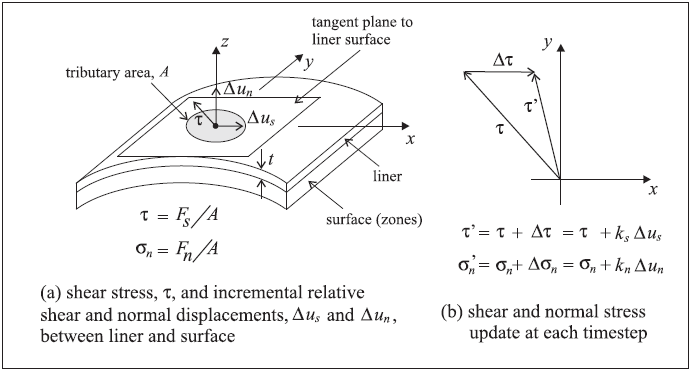
Figure 2: Idealization of interface behavior at a liner node
The normal behavior of the liner-zone interface (see Figure 3) is controlled by the normal coupling spring properties of (1) stiffness per unit area, \(k_n\), and (2) tensile strength, \(f_t\). The shear behavior of the liner-zone interface (see Figure 4) is cohesive and frictional in nature, and is controlled by the shear coupling spring properties of (1) stiffness per unit area, \(k_s\), (2) cohesive strength, \(c\), (3) residual cohesive strength, \(c_r\), and (4) friction angle, \(\phi\), and by the interface normal stress, \(\sigma_n\). If the liner fails in tension, then the effective cohesion drops from \(c\) to \(c_r\), and the tensile strength is set to zero. The total relative normal displacement, \(u_n\), continues to be tracked such that compressive normal stresses will again develop when the gap closes. Note that the coupling spring properties associated with each liner element are averaged at liner nodes.
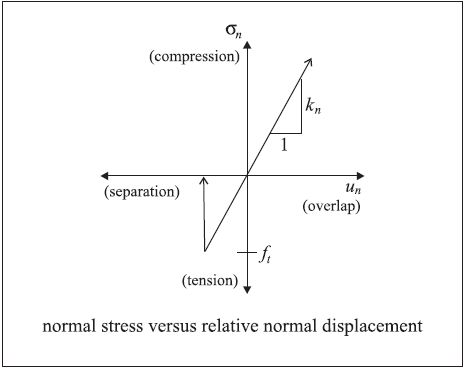
Figure 3: Normal-directional interface behavior for liner elements
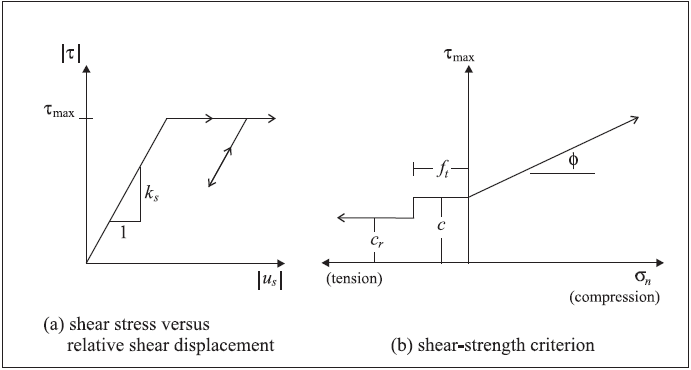
Figure 4: Shear-directional interface behavior for liner elements
In computing the relative displacement at the liner-zone interface, an interpolation scheme is used to calculate the grid displacement, based on the displacement field in the zone to which the node is linked. The interpolation scheme uses weighting factors that are determined by the distance to each of the zone gridpoints. The same interpolation scheme is used to apply forces developed in the liner-zone interface back to the gridpoints of the zone.
Liners support large-strain sliding (by setting the slide property to on), whereby the interpolation locations (used by the liner nodes to transfer forces and velocities to and from the zones — see Structural Element Links) will migrate through the grid when running in large-strain mode. This allows one to calculate the large-strain, post-failure behavior of a liner, whereby substantial sliding between the liner nodes and the zones occurs. At each liner node, if large-strain sliding is on and the tensile stress exceeds the interface tensile strength, then the link that joins this liner node to a zone surface will be deleted; however, if this node later comes back into contact with any zone face, the connection will be reestablished (via a new link with appropriate liner properties).
Embedded Liner Behavior
The liner structural element can also be made to interact with FLAC3D zones on both sides of the liner. Additional coupling springs are added to the embedded liner for this capability. (The default liner only provides a single link on each node, whereas the embedded liner provides two links on each node.) Independent properties are specified on each side of the embedded liner (side 1 and side 2). The embedded liner mechanical behavior is similar to the default liner behavior described above, except that the zone-liner interface is active on both sides of the embedded liner.
Response Quantities
Liner responses include stresses in the liner itself, as well as stress, displacement, yield state and loading direction in both the normal and shear coupling springs. The liner responses can be accessed via FISH, and
- printed with the
structure liner list
command,- monitored with the
structure liner history
command, and- plotted with the Liner plot item.
Refer to Shell-Type Response Quantities for a summary of the commands that support recovery of stresses acting in the liner itself.
Embedded Liner Response Quantities
Embedded liner response quantities are similar to the default liner response quantities described above, except that links or associated quantities can be associated with side 2 as well as side 1, or can be specified with structure liner history
command.
The Liner plot item may be colored differently on each side to help identify side 1 and side 2.
Properties
Each liner elements has 8 or 14 (if embedded) properties in addition to those common to all shell-type elements described in Shell-Type Properties. These properties control the shear and normal behavior of the liner-soil interface.
- coupling-yield-normal, normal coupling spring tensile strength (stress units), \(f_t\) [F/L2]
- coupling-yield-normal-2, normal coupling spring tensile strength on side 2 (stress units), \(f_t\) [F/L2]
- coupling-stiffness-normal, normal coupling spring stiffness per unit area, \(k_n\) [F/L3]
- coupling-stiffness-normal-2, normal coupling spring stiffness per unit area on side 2, \(k_n\) [F/L3]
- coupling-cohesion-shear, shear coupling spring cohesion (stress units), \(c\) [F/L2]
- coupling-cohesion-shear-2, shear coupling spring cohesion on side 2 (stress units), \(c\) [F/L2]
- coupling-cohesion-shear-residual, shear coupling spring residual cohesion (stress units), \(c_r\) [F/L2]
- coupling-cohesion-shear-residual-2, shear coupling spring residual cohesion on side 2 (stress units), \(c_r\) [F/L2]
- coupling-friction-shear, shear coupling spring friction angle, \(\phi\) [degrees]
- coupling-friction-shear-2, shear coupling spring friction angle on side 2, \(\phi\) [degrees]
- coupling-stiffness-shear, shear coupling spring stiffness per unit area, \(k_s\) [F/L3]
- coupling-stiffness-shear-2, shear coupling spring stiffness per unit area on side 2, \(k_s\) [F/L3]
- slide, large-strain sliding flag (default: off)
- slide-tolerance, large-strain sliding tolerance
These properties can be divided into strength (\(f_t\), \(c\), \(c_r\), \(\phi\)) and stiffness (\(k_n\), \(k_s\)) properties. Choice of appropriate strength properties should be relatively straightforward, as these correspond with measurable macroscopic strength properties of the real physical system. Choice of the stiffness properties is more complex and will be discussed below (refer to Interfaces for a more detailed discussion).
Typically, we want the liner-zone interface to be stiff compared to the surrounding material, but able to slip and perhaps open in response to the anticipated loading. For this situation, we simply need to provide a means by which the liner elements can slide and/or open relative to the zone surfaces. The strength properties are important, but the elastic stiffnesses are not. It is recommended that the lowest stiffness consistent with small interface deformation be used. A good rule-of-thumb is that \(k_n\) and \(k_s\) be set to ten times the equivalent stiffness of the stiffest neighboring zone. The apparent stiffness (expressed in stress-per-distance units) of a zone in the direction normal to the surface is
where: | \(K\) and \(G\) | = the bulk and shear modulus, respectively; and |
\(\Delta z_{\rm min}\) | = the smallest dimension of an adjoining zone in the normal direction. |
The max [ ] notation indicates that the maximum value over all zones adjacent to the liner is to be used (e.g., there may be several materials adjoining the liner). Note that (1) strictly applies only to a planar surface subjected to normal penetration. If the surface is curved, as is the case surrounding a circular excavation, the apparent stiffness should be increased by a factor of 10 to 100. For a particular problem, it is recommended that one confirm that the interface deformation (i.e., the displacement in the coupling spring) is small relative to the zone deformation. (The coupling spring displacement is obtained via the structure liner list coupling-normal
command; the zone deformation is obtained via the zone gridpoint list displacement
command.)
Example Applications
Simple examples are given to illustrate the use of liner.
A complete list of examples that use liner elements is available in Structural Liner Examples.
Commands & FISH
Was this helpful? ... | PFC 6.0 © 2019, Itasca | Updated: Nov 19, 2021 |